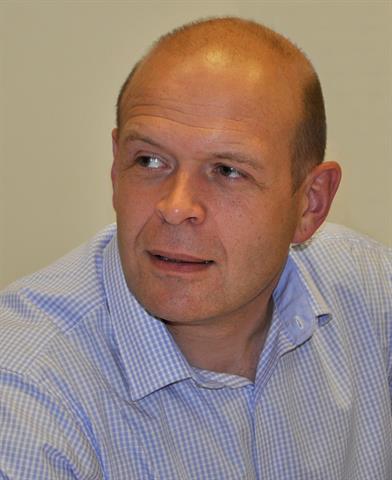 Stuart Taylor |
Stuart Taylor is a director of Mentor FLT Training Limited's Performance & Risk Management division. Mentor is the UK's leading provider of training and associated services for all types of materials handling equipment and workplace transport.
Today, at a workplace in the UK, at least one worker will be dealt a life-changing injury by a forklift. About three more will have accidents that keep them off work for a week, and there'll be more minor incidents than you can count.
The same thing will happen again tomorrow. And every day after that.
It's a grim kind of lottery, with catastrophic consequences - and not just for the employees themselves. Purely as a business cost, the price of an accident can be painfully high and goes far beyond the obvious aspects you might think of.
So, what does an accident really cost your business?
Legal costsThis is the part everyone thinks about. After all, the highest combined cost (fine plus court fees) for a UK forklift accident stands at £800,000. Even for a non-fatal accident, five-figure sums are not uncommon - not counting compensation to the victim or your own legal fees.
Plus, with the HSE focusing on supervision as key to reducing accidents, we have seen a significant rise in the number of prosecutions targeting management personally. According to HSE figures, the number of directors prosecuted under Section 37 of the Health & Safety Work Act in the five years leading up to 2010/11 rose by 330%, while during the same time period, successful convictions increased from 50% of cases to 81%. The maximum sentence is two years in prison or an unlimited fine.
Oh, and you'd better brace yourself for your future insurance premiums, too.
Lost working time - staff and managementIf an employee is injured, there's sick pay plus overtime to cover their shifts. And the lost time while the accident is cleaned up. And what about your time as manager, dealing with the legal fallout and HSE?
Meanwhile, there's a measurable fall in productivity when staff feel they're unsafe at work, and a poor accident track record makes it more expensive to find and retain good staff - not to be sniffed at, when Toyota Material Handling estimates every new fork lift truck operator costs in excess of £4,000 to recruit. New workers can be less productive, which could result in more accidents.
But in the real world, not every accident injures employees, or ends up in a prosecution. So let's talk about real costs you're paying out for, right now.
Damage to stock, machinery, fixtures and fittingsForget about big accidents and court cases for a minute. Think about all the minor accidents, mishaps and scrapes. Dropped loads. Bumped racking. Dented trucks. Those costs come straight off your bottom line - and the scale might shock you.
British businesses spend millions of pounds a year simply repairing racking and forklifts, as well as replacing needlessly damaged stock.
Toyota estimate 5% of the total cost of forklift ownership is unbudgeted and unscheduled repairs outside of the contract. To put that in context, as a rule of thumb, for every £1 you spend on truck repairs, it is estimated that between five and twenty times that amount (dependant on the industry sector in which you work) is caused in damage elsewhere - racking, buildings, stock and the like.
Even a dropped pallet of coffee can have the retail price of a small car.
Toyota say a typical pallet is handled six times during the distribution process - the more a pallet is handled, the greater the risk to the pallet.
Real costs, right nowOf course, it's right to protect employees. But thinking of safety as an overhead cost to prevent some bigger catastrophe is really missing the point: unsafe practice is costing you money today.
Too many companies simply write off huge bills for damage to forklifts, stock and racking as if they were an inevitable business overhead. They're not. According to the Institution of Occupational Safety and Health (IOSH), 70% of workplace incidents are preventable by good management. Here at Mentor, we believe 70% of costs are too.
Safe practice isn't really a precaution at all. It's an opportunity to increase your profitability.