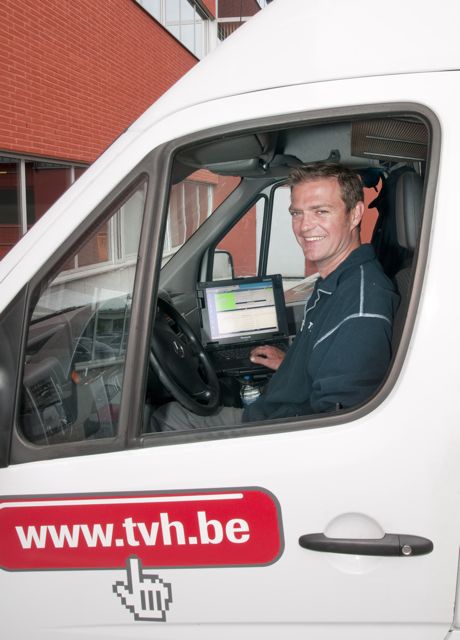 The software offers a new way of communication between TVH office staff and mechanics on the road. |
TVH has invested two years into developing a planning software for its Service & Repair division that it says is paying off in terms of cost savings and higher work efficiency.
TVH spokeswoman Debbie Manhaeve says the new system reduces TVH's labour costs by allowing people to work more efficiently.
She explains that the system offers a new way of communication between the back office (the TVH planner) and the mechanics on the road.
For example, a customer who requests a forklift repair will immediately be told by the TVH planner the exact time the engineer will arrive. The availability of real-time information reduces the need for phone calls between the parties.
The engineer will use a device on site which incorporates GPS, email and service information, and which communicates with the TVH network via a mobile 3G network. This allows the engineer to consult maintenance manuals online and to call up the maintenance history of a machine. He can also pass on his job status to the planner and receive details for a new assignment via the central device.
The planner gets map locations for the engineers and can call on the closest engineer to meet a customer request. He can also discern the job status of the engineers and so can inform the customers of any delays.
The system is expected to save the company EUR25,000 (USD35,000) annually and boost the Service & Repair division's efficiency by 10%.