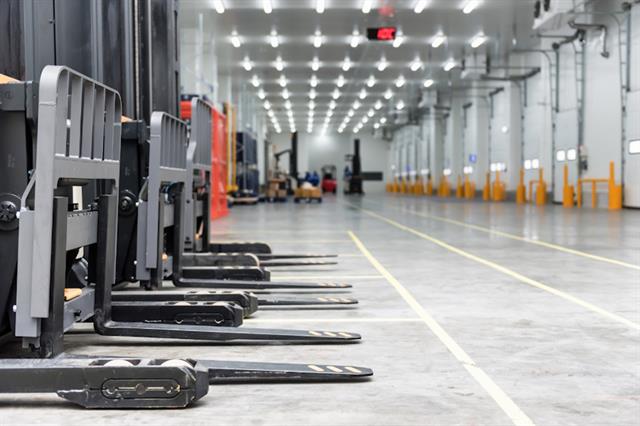
Tools designed to facilitate the management, tracking and maintenance of forklifts, fleet management systems have much to offer in terms of safety and efficiency.
Employed thoughtfully and used to their full potential, they have the capacity to reduce operating costs and the all-important bottom lines of materials handling operations.
Here, the phrases ‘employed thoughtfully’ and ‘used to their full potential’ are key, because not all types of fleet management are suitable for all types of operations. Choosing the right system involves considering several variables, including size of business, fleet size, product type and more.
“There have never been so many fleet management solutions to choose from and that makes the selection process more complex for customers,” says Arnaud Bollini, general manager of fleet management consultancy B. Forklift.
“The most important for the future user is to start by looking at the needs or pain points and what the situation could be tomorrow.”
Fleet management consultancy, B. Forklift favours a holistic approach to strengthen operational and financial performance
According to Bollini, defining metrics (including economic, operational, environmental and social variables) is essential to assess the initial situation and set objectives.
“Beware of the ‘wow effect’ and stay focused on the basics,” he warns.
“Sometimes we see customers' eyes light up when they see a hyper-developed solution with a wide range of functions. But you don’t always need them.”
“Our recommendation is not to go too fast, but rather to start small, generate quick wins and get teams on board with effective, easy-to-use solutions. ‘Done is better than perfect’ should be the motto when it comes to fleet management systems.
“Once they’re installed and working it’s always possible to upgrade or activate new functions.”
According to Bollini, software systems shouldn't be ends in themselves. “Companies must allocate resources and define processes to transform the data into a performance plan. And this is the real weak point with increasingly lean organisations,” he says.
Intelligent vehicle terminal
Assuming these considerations are dealt with, the best fleet management systems have much to offer in terms of reducing operating costs. Hangcha FIMS, an intelligent vehicle terminal deployed on industrial vehicles, is a good example.
“The system is capable of monitoring the performance of vehicles and equipment, as well as understanding the fault codes reported by the vehicles,” says Zhang Yaming, senior engineer at Hangcha.
Hangcha FIMS is capable of monitoring the performance of vehicles and equipment, as well as understanding the fault codes reported by the vehicle
“This enables manager and maintenance staff to take appropriate corrective actions, thereby reducing the occurrence of unexpected faults and minimising repair downtime.”
Thanks to its real-time tracking capacity, the system can monitor the operating status and efficiency of material processing equipment as it happens. This includes scheduling efficiency, dispatch efficiency, production efficiency, utilization efficiency and cargo loading efficiency of both vehicles and drivers.
“By collecting and analysing data, managers can promptly identify potential issues with equipment and take appropriate measures for adjustments, maximising the utilisation of the equipment's capabilities and enhancing productivity,” notes Yaming.
At the same time, the system’s preventative maintenance capability allows management to develop plans based on equipment usage and maintenance history.
“Regular maintenance and upkeep can reduce the risk of equipment failures and lower repair costs,” says Yaming. “Meanwhile, the system can monitor battery usage, abnormal charging and overall energy consumption to reduce battery wear, prolong battery life and achieve cost reduction goals.”
By collecting and analysing equipment data, managers can gain a clear understanding of which drivers and vehicles are causing a decrease in overall fleet efficiency; and of which drivers are experiencing more safety issues (such as abnormal vibrations or speeding). In turn, this allows for targeted management and attention to those drivers and vehicles.
Enhanced equipment utilisation
Sapphire, a fleet and safety management solution from GemOne, empowers fleet owners to enhance warehouse safety and compliance, streamline operator management and boost fleet efficiency.
Sapphire is designed to help materials handling operations manage equipment in a safer, more efficient and regulatorily compliant manner
“The system is designed to help equipment dealerships to minimise machine downtime, enhance customer satisfaction and use one system for all makes and models of machines,” says Samuel Silva, GemOne’s executive vice president of the Americas.
“With features such as pre-start checklists, access control, impact reporting and proximity warning, Sapphire helps you manage your equipment in a safer, more efficient and regulatorily compliant manner.”
As a business unit of TVH Parts, GemOne’s fleet management telematics are backed by more than 50 years of experience in industrial machinery, serving more than 100,000 connected assets globally.
As used by Atlas Toyota Material Handling, an equipment dealership in the American Midwest, GemOne's Sapphire telematics solution was able to successfully optimise fleet management, enhance customer satisfaction and reduce costs.
“Through Sapphire, they gained valuable insights into fleet performance, safety compliance and operational efficiency, addressing challenges such as data collation, safety checklist management and key hours tracking,” says Silva.
“Their partnership with GemOne facilitated improved customer service, advanced business insights and enhanced support, ultimately strengthening Atlas’ position as a leader in equipment dealerships in the materials handling industry.”
“By leveraging real-time data and advanced analytics, businesses can unlock new levels of efficiency, safety and profitability in their warehouse operations.”
The human factor
Presented with the impressive data collection capabilities of the latest fleet management tools, it’s important that businesses don’t forget that making sense of that data is equally important.
Fleet Team Inc. seeks to empower its clients to make their own data-driven decisions that reduce downtime
“It’s not just about the fleet management systems, it’s about the people interpreting the data that those systems are collecting to create actionable plans,” says Doug Riddle, president of Fleet Team Inc., a brand-independent consulting partner focused on empowering businesses to optimise their fleet management practices.
“Without the people, you just have tools collecting data. Now you have a lot of data but no actions to take to optimise your fleet.”
As Riddle explains, Fleet Team starts by forming partnerships with the client. From there, the next step is to produce an in-depth analysis of the current fleet, operations, cost analysis and throughput.
“During our evaluation, our experts focus on safety, different cost-saving opportunities, application analysis and total cost of ownership for the entire fleet,” he says, adding that his team understands the importance of empowering clients to make their own data-driven decisions that minimise breakdowns and reduce downtime.
“Any company's most expensive asset is the one they don't need. Our platform provides factual data to evaluate the assets that are not needed, the flexibility to move assets to different locations, the tipping point when assets become more expensive to keep and the right time to replace them,” says Riddle.
Making the most of data
The best fleet management systems, such as JLT Insights, are designed with this type of user-friendliness in mind.
According to Eric Miller, CEO of JLT Mobile Computers Inc., the software combines functionalities from mobile device management systems (MDM) and traditional fleet management systems and comes with the ability to drill down in the data gathered about the registered devices, vehicles and access points.
Unlike other solutions on the market, JLT Insights is embedded in the JLT6012 Series rugged forklift computers
“It’s designed to monitor key areas in warehouse operations and provide real-time alerts to improve forklift productivity,” says Miller.
Unlike other solutions on the market, JLT Insights is embedded in the JLT6012 Series rugged forklift computers – making it easier than ever to get going with relevant data capturing.
“Thanks to an array of sensors embedded in the JLT6012 Series of rugged computers, you can capture real-time operational dynamics and compare, contextualise, display and disburse this data using the JLT Insights dashboard, enabling tailormade analysis for optimising IT and warehouse management. Since the software is specifically designed for use on the JLT6012 computers, the complete solution from JLT ensures trouble-free integration,” says Miller.
According to Miller, it represents a game-changer in the realm of forklift management software, precisely because of its capacity to monitor, analyse and optimise critical operations.
“By leveraging real-time data and advanced analytics, businesses can unlock new levels of efficiency, safety and profitability in their warehouse operations,” he says.
Collaboration & training
The final word on fleet management systems and their cost cutting capacity goes to Ilie Haures, chief executive officer of Forklift Safety Systems.
Forklift Safety Systems is focused on partnering with its clients to make the most of its fleet management system
According to Haures, as it stands, the main problem with forklift management is not that the available systems are in any way inadequate or not up to the tasks they are expected to perform.
The major issue is that they are purchased with the assumption that, after usage data is accessed and interpreted, it will result in one-on-one training sessions with the relevant forklift drivers, as a way to improve future performance.
“But let’s be honest…this happens in less than 10% of cases,” says Haures. “Warehouses are always busy. People are coming and going, so having a plan for these specific use cases is close to impossible.”
According to Haures, Forklift Safety Systems takes a deliberately different approach. “Our purpose as a company is to continuously train the forklift driver, using our Smart Forklift Technology,” he says.
In other words, he says, the company aims to train drivers using a ‘car driving school’ model, rather than a traditional forklift training model. The main difference between the two, is that the former involves an instructor sitting in the car alongside the driver, giving tips and instructions.
“Our Safety Fleet Manager does exactly this, using an acoustic warning each time the driver speeds, applies the brakes harshly or accelerates too quickly,” says Haures.
“We want the driver to feel safe driving a forklift with our Smart Forklift Technology…exactly like having an instructor watching and continuously improving our driving style.”
Concluding, Haures adds that Forklift Safety Systems’ main focus is not on the software itself, but “the team behind the software”.
Like all the systems and suppliers mentioned above, the company is all about entering into effective partnerships with its clients to unlock the true potential of these impressive systems – and in so doing – to reap the benefits in terms safety, efficiency and business success.
Find out more about the efficiencies and offerings fleet management systems from our contributors can provide, in this dedicated Virtual Showroom.
For this report we interviewed the following industry specialists: