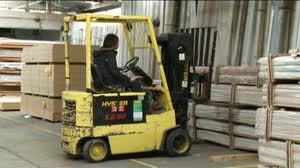 Drivers should be trained on the equipment they'll be using, in the environment in which they'll be using it. |
Rob Vetter is technical director and managing partner with the Ives Training Group, in Blaine, WA, USA, a leader in North American mobile equipment training systems since 1981.
As any coach in the sporting world will tell you, whether it's your swing, throw, stroke or shot, the follow-through is every bit as important as the wind-up. In the same vein, any industrial mobile equipment trainer that's worth their salt will tell you the job isn't done until operators have demonstrated competence on the type(s) of equipment they are actually assigned to operate. That is a trainer's follow-through.
I have noticed a rather frightening trend unfolding out there in which seemingly reputable training providers are doing general training and evaluation, but implying that it is specific training. In some cases, these training programs are being delivered off-site - which right there is a red flag since training must be equipment- and site-specific and evaluation must be conducted in the workplace as per federal and state operator training regulations.
On the surface, nothing appears to be lacking from an employer's perspective as they are being told that their operators are getting trained and evaluated as they should and that they're covered. But what is actually happening in many cases is:
* The initial basic training is too general, in that the number of topics addressed is abbreviated and subjects are not covered in detail, nor is it specific to any particular type of forklift.
* The practical evaluation is conducted using equipment that may or may not be used by the trainee at his or her worksite. Given the amount of variation in the operational design of many forklifts and the fact that evaluation in the workplace is mandated by regulation (in the US), this can present significant risk potential, not to mention liability for employers.
* The site- and equipment-specific training is left to the employer and/or user to deliver after the train¬ing provider completes the general training and evaluation. This is just wrong on a number of levels.
* Employers often do not look past the fact that an operator returns to the worksite with a ticket or certificate of some kind which, in their minds, qualifies the holder to operate anything, regardless of what it was they were evaluated on. This usually means that the specific training never takes place.
* If model-specific training and/or evaluation actually does take place with the returning operator, it is often hastily delivered by unqual¬ified personnel that have no idea of what the operator was trained in or how he/she was told to operate the equipment.
I suppose that some training providers are doing things this way to offer a quick and cheap route to qualifying operators - always a big selling point with busy contractors and employers. But, is it really quicker or cheaper?
If I were a contractor and I chose to get a bunch of people trained up on a forklift, here's the way it would play out.
I would have to round up all of my people that could possibly be directed to operate the unit, or as many of them as I could spare and send them off site for training. They would likely be gone for at least six hours - for all intents and purposes, a full day. When they returned the next day, I would need to "familiarise" them with the machine(s) they will actually be asked to operate on site. I would also need to bring them up to speed on the local hazards and any site-specific rules and company polices related to their job(s).
I need to have them evaluated operating the machine they are assigned to because I want it on record that they have demonstrated competence to a qualified person in the workplace, as per mandatory regulatory requirements(whether the person to whom the operator demonstrates competence is qualified to evaluate the demonstration is another issue I need to deal with). All of this training and evaluation after the original program delivered by the training provider is time and money out of my pocket and by now I'm feeling pretty frustrated.
Employers could save themselves a lot of time, money and potential grief by making sure they provide site- and equipment-specific training, regardless of whom they choose to deliver it and that performance evaluations are conducted in the workplace using the same type of equipment the operators are actually assigned to operate.
Not only is this the mandated approach (in the US, at least), but it's just the right thing to do to make sure everyone goes home at the end of the day.