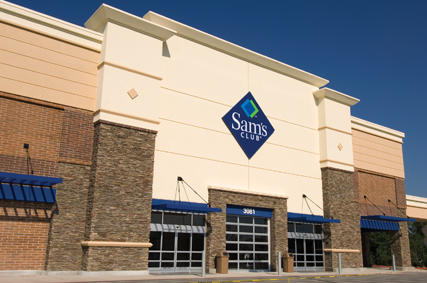 Sam's Club, Fayetteville, Ark |
By Roger Renstrom
Wal-Mart Stores Inc is working with forklift providers and others to capture the potential benefits of radio-frequency-identification (RFID) technology.
In the US, "we have 1,300 Wal-Mart stores out of 3,600 (locations) equipped with the technology to some extent" but not yet on forklifts, Wal-Mart spokesman John Simley tells
Forkliftaction.com News.
While two forklifts at a subsidiary have been updated, no forklifts in the Wal-Mart stores segment have a critical wiring retrofit that manufacturers or their service centers are expected to perform. "We have to power the unit and make sure that it does not interfere with the hydraulics or machinery that operate the system," he says. "So far, very little retrofit work has been done. All forklifts will need to be equipped with the technology."
Crown Equipment Corp of New Bremen, Ohio and Raymond Corp of Greene, New York are primary suppliers of electric forklifts to Wal-Mart, Simley says.
The manufacturers have tested technologies with and for Wal-Mart and others, conducted pilot runs and designed equipment modifications over several years.
Raymond, for instance, engineered a pouch within a forklift's load backrest to accommodate either of two prominent styles of tag readers and also designed ways to route power cabling to the reader. "We can outfit our trucks off the line," but, so far, the system has not entered the commercial market, says Joe Lafergola, manager of fleet services for Raymond national accounts. "Wal-Mart was a driving force that moved the project along."
Simley says the systems "have to regulate the power so they do not fry the reader" or hinder the ability to read Generation 2 electronic-product-code (EPC) tags. Reader makers specify parameters for the type of power supply to use.
Further, the equipment must have the ability to read a specific tag "so it is not reading tags from 60 different bags," he says. The EPC family of coding schemes uses RFID technology and exists as a way to track goods using hand-held readers and at stationary portals such as dock receiving bays, transition doors, compactors and bailers.
Orders for forklifts will incorporate newly designed specifications for the recessed compartment for the forklift-mounted reader and suitable conduit to contain the wiring, Simley says.
Wal-Mart's massive logistics operations are making progress with EPC implementation and offering "an ability to move a volume of products effectively and efficiently with a minimum of errors," he says.
Within another market segment, Wal-Mart subsidiary Sam's Club intends to use EPC technology in 591 locations in the US and six in Canada. "Sam's Club can implement the technology in a faster way" with its focus on tagging pallets rather than the Wal-Mart practice involving tagging of individual high-value products or mixed pallets, Simley says. The Sam's Club business segment may have 5,000 stock keeping units (SKUs) versus a Wal-Mart super-store's 100,000 SKUs.
"We have (EPC tag) readers on forklifts at two Sam's Club locations", he says.
On January30, the Sam's Club distribution center in DeSoto, Texas began requiring upstream suppliers to apply EPC labels on pallets. Sam's Club levies a per-pallet fee up to USD3 for non-compliance. The requirement is a way to accommodate suppliers yet to implement their own technology solution.
Sam's Club centres in Kansas City, Missouri; Searcy, Arkansas; Dayton, Texas; and Villa Rica, Georgia will add the pallet tagging requirement in October, and the 17 remaining Sam's Club distribution sites in the US will come aboard in January 2009. Having a reader on a forklift enables a centre's operations staff to know what is on a tagged pallet and into which slot that pallet was placed.
A Sam's Club schedule calls for suppliers to progress steadily toward case-level and sellable-unit-level EPC tagging.
Bentonville-based Wal-Mart employs more than 1.9 million globally and reported profit of USD11.28 billion on sales of USD344.9 billion for the fiscal year ended 31 January 2007.