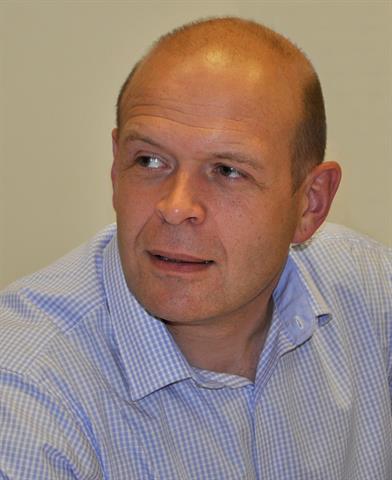 Stuart Taylor |
Stuart Taylor is Managing Director of Mentor FLT Training Limited, the UK's leading provider of training and associated services for all types of materials handling equipment and workplace transport.
Behind every success story is a strong leader - driving it forward - and safety improvements are certainly no exception, according to
Stuart Taylor.
At the 2015 National Fork Truck Safety Conference, special emphasis was placed on the need for a holistic approach to safety, coupled with strong leadership, with the HSE pinpointing the importance of the manager's role. Fittingly, the FLTA has chosen to continue to focus on this and has made Leadership and Ownership the theme of this year's upcoming conference.
Creating confident and capable leadersThe nature of logistics work means that managers and supervisors often have a number of responsibilities to juggle during a typical working day, but most critical is the substantial influence they have on the site's culture and its norms - for better or worse.
Although many companies commit heavily to developing their safety cultures, the message from the materials handling industry's leading thinkers is clear: without confident and competent leadership, your efforts can quickly come undone.
You see, while quality forklift training teaches operators to work safely, sustaining this in the short and the long term is only possible if supervisors have the skills, knowledge and self-assurance to actively ensure that standards are upheld.
Quite often, this level of expertise is underestimated and simply mistaken for 'common sense'. But that couldn't be further from the truth.
These skills aren't just picked up on the job. More than half of the 1,500 men and women we have met while delivering our Managing Forklift Operations course had never driven a forklift before - let alone received any sort of formal training. What's more, nine out of 10 were not aware of their legal responsibilities - as companies or individuals. Nor were they aware of the severe consequences of an accident that results in prosecution.
In its latest edition, the
L117 Approved Code of Practice for Rider-operated Lift Trucks specifically outlines the role of supervisors and their responsibilities for safety. Whilst they don't need to learn how to operate a truck, they do need to understand the risks involved and how to reduce these down to a minimum by actively promoting best practice.
Supervisory staff with little understanding of the risks involved in materials handling - not to mention the benefits of a safe and efficient operation - are poorly placed to safeguard their employees ... and their businesses.
Trained managers are equipped with the knowledge, skills and understanding they need to proactively manage the use of forklift trucks in the workplace - effectively, safely and legally - in full compliance with L117, the definitive guide to forklift truck operations.
More than avoiding accidentsBut good supervision does more than prevent accidents. It's no surprise that the most safety-minded companies are commonly among the most cost-effective.
By training your operators to be safe and your managers to manage safely, your team becomes more efficient and can avoid costly accidents and disruption, saving money that contributes directly to your bottom line.
Take damage costs, for example. Some companies regularly write off millions of pounds of stock and racking damage each year. Other businesses actively incentivise their managers and supervisors to keep damage levels low, and, while this is a good starting point, the fact that many companies have a target budget for these things means they implicitly accept that damage and the associated costs are inevitable.
Rather than a mindset of damage limitation, we encourage companies to challenge the practices and attitudes at the root of the problem. By equipping your managers with the skills to proactively promote and maintain an environment of best practice, they can champion safety and encourage others to do the same, keeping your site safe and productive.