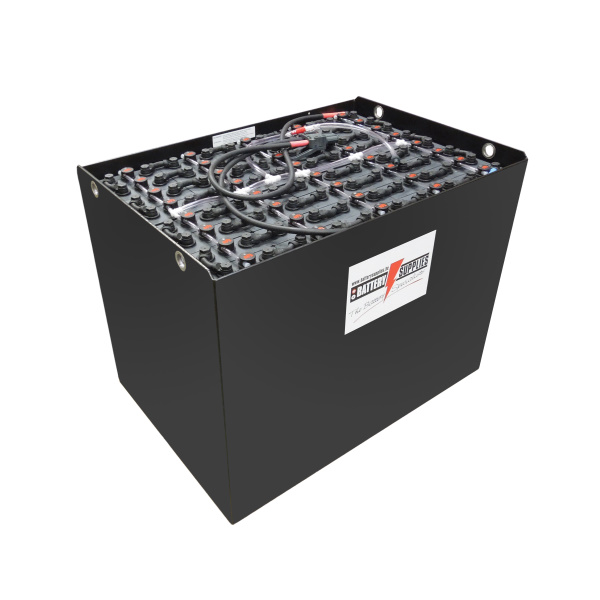 Components and materials may be in short supply |
By Allan LeibowitzThe materials handling market is starting to feel the battery shortages facing the automotive industry.
There are widespread reports that automotive battery manufacturers are struggling to source key materials, notably cobalt and lithium, while vital electrical components are also in short supply.
Andy Napoleon Hill, marketing director at battery maker Philadelphia Scientific, says at the moment, the materials in shortest supply are electronic components. "We've got a pretty wide range of products, so we've been able to innovate our way around some of the stocking issues that we face," he explains.
Maurizio Pelloni, sales manager at PBM, says his company is also facing shortages of electronic components, "but the main problem is raw material prices and availability".
He admits the shortages are affecting the Italian charger manufacturer, but "not drastically"; however, the future situation "does not look easy".
Philadelphia Scientific, meanwhile, has been stock piling and innovating its production methods and materials to meet its current obligations. "Talking and listening to our customers has always been our strong point, so we've been able to manage expectations and have kept everybody informed in regard to delivery dates," according to Hill.
Tim Karimov, president of OneCharge Lithium Batteries, says his company is fully stocked with all materials and supplies required for production.
"We have not experienced and we do not expect to experience any shortage-induced delays," he says, although he does admit to "experiencing the higher prices and longer lead times for steel, which may cause the need for a price increase across the industry, similar to what's happening with the forklift OEMs right now".
"Also, we're hearing through our dealer network that some battery makers are already experiencing longer delivery times. OneCharge has just moved to a new facility and increased its production capabilities to meet current and future demands," he adds.
Hill notes an increase in demand at Philadelphia Scientific, "which we've been able to meet!".
"Li-ion batteries not only require the raw materials, they require a lot of electronics to make sure they don't overcharge, overheat and over-discharge. The electronics component lead time has severely hampered the viability of changing to lithium for a lot of businesses, so they've been looking to ways to improve their current fleet of lead acid batteries," he explains.
"Lead acid batteries may not be glamorous, but they are dependable and economically more viable"
Another factor helping the lead acid market at the moment is the high level of recycling. "Lead acid batteries are also 99% recyclable so won't be hampered by the shortage of electronic materials and subsequent increase in price that many Li-ion manufacturers and their customers are facing," he says.
Pelloni sees price increases as inevitable and predicts that the remainder of 2021 will be "a very difficult year". Delays will also be constant as PBM deals not only with the supply-side challenges, but also with a drastic increase in sales and orders, he points out.
OneCharge's Karimov remains optimistic: "We are, overall, very happy with the current situation, in spite of some of the cost increases we've had to absorb. We are exceeding our expectations so far in 2021 and with the improvements we have planned, we should be able to continue at this level well into next year," he says.
Hill's advice to everyone in the materials handling market is to focus on communication. "Speak to your suppliers, speak to your customers and speak to your staff. The worst thing companies can do is over-promise and under-deliver," he suggests.