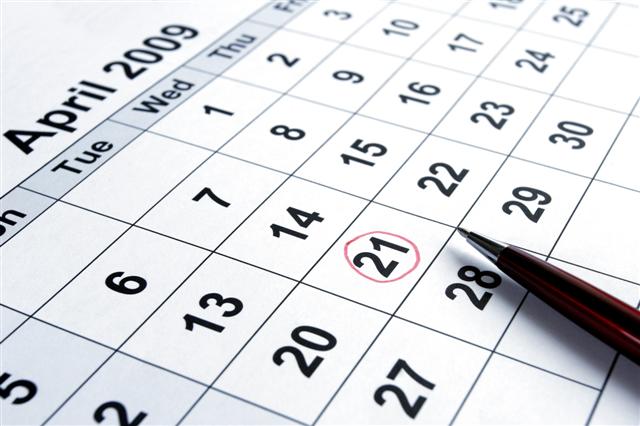 Over the past 18 months or so, we have seen what can happen even to large, seemingly strong companies. PHOTO: SHUTTERSTOCK |
Rob Vetter is technical director and managing partner with the Ives Training Group, in Blaine, WA, USA, a leader in North American mobile equipment training systems since 1981.
Congratulations, you made it through the first quarter of 2010 with the rest of us! This is no small feat as, over the past 18 months or so, we have seen what can happen even to large, seemingly strong companies that did not have the ability make the changes in attitude and practice needed to stay financially healthy - or to even recognise that such changes were needed.
The changes, as I see them, are due to several drivers such as:
* Economic Impact: Most companies that "get it" recognise that investing in quality training as an integral part of an overall safety program that includes diligent monitoring, adjustment and enforcement is just good business from a profitability standpoint.
* Language and Literacy: As the workforces of the US and Canada continue to expand with workers whose primary language is not English, training providers must be able to accommodate the demand for training materials in other languages. Literacy issues stemming from a trainee's reading and writing abilities pose a particularly difficult challenge to a trainer who must be willing and able to abandon traditional teaching methods in favour of more visual and interactive techniques.
* Keeping Up:
o The past 10 years have seen more changes in regulations and standards than the 30 years before. While changes within federal regulations have remained relatively conservative, changes to state and provincial regulations have been anything but. Trainers must be aware of this and keep a constant finger on the pulse behind these changes, and adjust accordingly.
o Manufacturer innovations in equipment design, construction and operation are moving ahead faster than ever before. Every model year, new and improved operational controls and systems add to those of the previous year - to the point where an operator with past experience on a given piece of equipment may have a significant difficulty in efficiently operating the 'same' piece of equipment today.
* Zero Tolerance: Regulatory agencies are growing more and more intolerant of employers who repeatedly and/or flagrantly contravene the rules. With record fines recently issued and aggressive enforcement policies, employers are under greater pressure than ever to get their people properly trained .
* Generation X: The 18-year-olds graduating from high school this year grew up in a completely different world to the one in which most of us did. Many young people today have great difficulty focusing in traditional classroom settings where reading and writing are core required skills and, since they never got to hand their parents tools while working on the car, or use those tools to tinker with things like we did, the general mechanical aptitude of the young today is weak. This presents another challenge to the modern trainer as many things taken for granted as common knowledge 'back in the day' are ancient history today.
There is no escaping the fact that the world and everything in it is changing, and people must change with it. But these things have always been changing so everything is humming along as it should. Change is not something to be feared but embraced; otherwise people will soon be talking about you in the past tense.