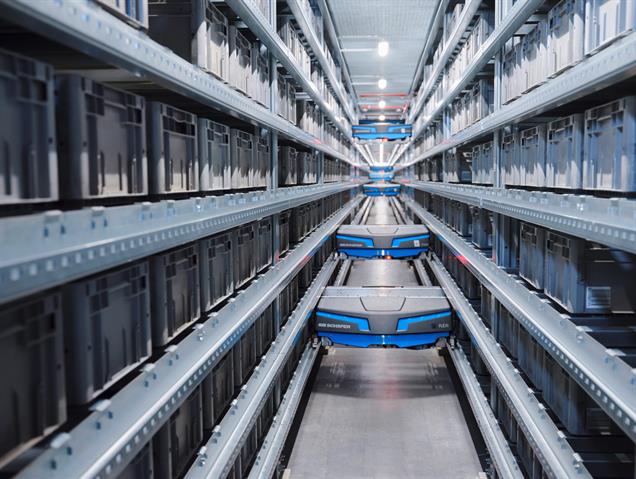 SSI Schäfer has added automation for VVA Group |
The VVA Group, part of Arvato Supply Chain Solutions, has modernised and expanded its distribution centre in Guetersloh during ongoing operations. An automated shuttle warehouse with order picking system has been built in the existing facility by long-time partner SSI Schäfer.
The new shuttle solution is a further step in the digital strategy with which Arvato is currently driving forward the automation of its worldwide locations.
The trigger for the capacity expansion was, on the one hand, the business growth of VVA in recent years. On the other hand, the business is characterised by a significant increase in picking intensity. As a partner and service provider, the company delivers media products from its three German locations in Guetersloh, Verl and Gilching to retailers and end consumers worldwide for more than 200 clients. In the central logistics centre in Guetersloh alone, about 70,000 different items are stored - ranging from books, CDs and DVDs to magazines, calendars, stationery and toys.
"With our existing system, which is already designed for very high performance, we have now reached the limits of our capacity," explains Harald Horstmann, vice president publisher at Arvato Supply Chain Solutions. "We wanted to continue using the existing system and not invest in a completely new solution. That's why we decided to modernise and expand together with SSI Schäfer."
The new storage and order-picking system was designed for a throughput of 16 million articles per year in an area of only 900 sqm. A highly dynamic modular shuttle system with around 40,000 bin locations was developed.
The new shuttle warehouse is located in a 24 m high extension directly next to the existing 60,000-pallet high-bay warehouse and is designed according to the patented 3D-Matrix Solution from SSI Schäfer.
A particular challenge was the system expansion during ongoing operation, which took place in three steps: First, the order start in the old system had to be relocated and further automated. In a second step, the direct conveyor connection of the fully automated high-bay warehouse to the existing and future storage and order-picking systems took place. The third and most important project step was the construction of the shuttle warehouse including the connected workstations. Business was not affected by the project work at any time.
The system has already passed its first test, allowing VVA to handle its largest order volumes since the company was founded in response to rising demand during the COVID-19 pandemic.