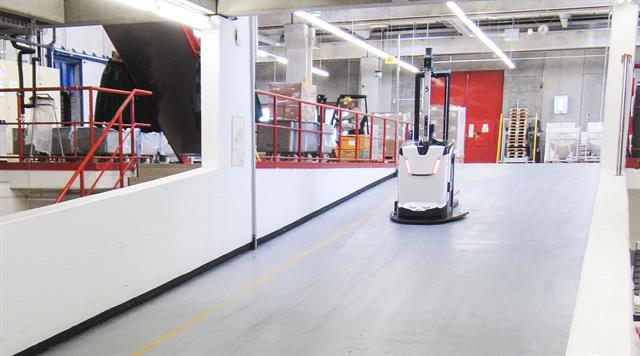 The Rocla AGVs have earned their place through efficiency in the Seeberger GmbH factory in Ulm during past two years. |
The leading producer of dried fruits and nuts Seeberger GmbH in Germany has built up its transportation automation using Rocla's Automated Guided Vehicles (AGVs).The new raw material hall at Seeberger GmbH in Ulm was opened during the summer of 2013. The new hall with high shelves is connected with a bridge to the production halls.
The number of the products transported daily is big and it is cost effective to take care of the logistics with an automated transportation system. Automation was not only needed for the transportation of the finished goods, but also for the delivery of raw materials to the packing machines. The AGVs showed to be the best logistic system for this task. Now five
Rocla AGVs transport raw materials from the Seeberger factory warehouse to the production halls.
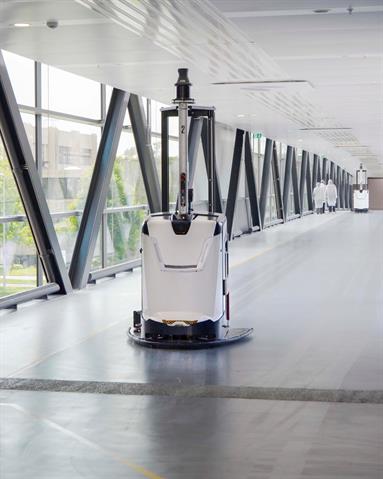 The return on investment for the Rocla AGVs is rapid. |
Fruit and nut trundles are not very heavy and Seeberger chose the compact
Rocla ATX12 trucks for the transportation tasks. The automation system is built up on the MetRo warehouse management system from
Rocla Solutions Oy.
The Seeberger GmbH factory in Ulm employs about 500 workers. The Seeberger family business will soon be able to look back on 170 years of tradition as a company. In the past decades the corporation has grown rapidly. It is the leading producer of the dried fruits and nuts in Germany, and also known for its quality coffee products. In November 2012 Seeberger received the "Mark of Century" award and in 2014, as also the year before, the "Top-Mark 2014" award from the grocery branch magazine Lebensmittel Zeitung in Germany.
AGVs are safe and effectiveProject engineer Marc Eberhardt is very satisfied with the
Rocla AGVs. He says that the AGVs are both reliable and effective.
'Here in Ulm we have a warehouse automation system with high shelves. This in combination with the transport efficiency of the
Rocla AGV trucks guarantees that the right things are always in the right place on time. This way we also have a constant, real-time overview of the warehouse and the material flow', Eberhardt explains.
Marc Eberhardt is one of Seeberger's four project engineers. He has been working at Seeberger for two years now and he was involved in the deployment of the AGV system. The co-operation between
Rocla and Seeberger has worked well. The AGVs came readily programmed from Rocla, and the transportation logistic strategy was planned by Marc Eberhardt.
The AGVs were taken into use through a thorough process. 'First we had a profound planning phase, which was followed by a testing phase. Then we took the AGVs into use gradually. We invested enough time in all the phases, so that the result would be the best possible. The system has been working perfectly, and we have needed hardly any corrections', Mr. Eberhardt says proudly.
The initial reservations of workers were swept away when they saw how surely, safely and effectively the AGVs operated. During the two years of AGVs working at Seeberger, there have been no accidents.
The AGVs are reliable workersThe
AGVs are programmed to go to the charging station automatically when their working schedule allows it. Under normal circumstances the battery usually runs a whole work shift at a time. The AGVs are praised for their quietness and low emission rates. The traditional forklift trucks are noisier and also more exposed to accidents due to human error.
The AGVs use laser triangulation for navigation. In the operational area there are laser reflectors which are scanned by a laser scanner on the trucks. The system knows all the time exactly where the AGVs are on the warehouse. When the Seeberger AGVs transport goods from or to the warehouse, they are coordinated via Wi-Fi network.
The
AGVs have scanners which recognize if there is someone or something in front of them and are able to drive around them. The AGVs usually move almost silently, but when they recognize someone in their way, they stop and use audible signals and warning lights for alert.
The AGVs move quite slowly around the warehouse, but constant movement makes them effective. 'The automatic transport vehicles do not need coffee pauses or holidays', says Marc Eberhardt, who estimates that the trucks pay themselves back in 3 to 4 years.
Special ramp for the AGVs
The specialty of the Seeberger production facilities is a ramp with a 9 % angle, and the AGVs use the ramp to move goods. The ramp floor is covered with a special coating, for more effective friction and for optimal breaking power.
Rocla and Seeberger developed a special detection system for the AGVs to help them to move on the ramp. The system, which slows the trucks down on the ramp, uses a magnetic switch which works through magnetic molding built in the floor. This system also reassures that the AGVs don't drive too fast on the ramp.
| See Rocla Oy on 21st Century Television |
For more information on Rocla's comprehensive AGV solutions please visit www.rocla-agv.comROCLA SOLUTIONS OYEmail: Send a message
Web: www.rocla-agv.comAGV Sales: +358 20 7781 332
AGV Services: +358 20 7781 312
P.O. Box 88,
FI-04401 Järvenpää,
FINLAND
Visit the Rocla ShopFront