Even with near-perfect care and maintenance, every forklift tire has its expiration date, some sooner than others. That’s when it comes down to tire design and composition. We know what you’re thinking, “it’s just rubber, what difference does it make?”
Using forklifts wears on the machine and the many components within it. Of all these moving parts, none experiences wear and tear quite like forklift tires. Below, we explore the importance of tire performance and discover a fascinating new technology that is helping material handling pros supercharge their efficiency.
How does forklift tire performance impact material handling efficiency?
It’s no trade secret that the performance and reliability of forklifts has a direct impact on warehouse operations. Across a fleet of forklifts, day-to-day efficiency relies on the equipment to move products without a hitch.
Efficient and consistent performance means that forklift tires are properly maintained and used to reduce wear. Forklift tires are in constant motion, piling on thousands of hours of use. Even the best operators and forklift drivers will grind their tires down to the point of replacement.
With that degradation of the tire, each forklift becomes less and less efficient with each moment of use. Whether it’s heat build-up, physical damage such as chunking, or overloading, tires are more susceptible to wear, reducing their performance, and decreasing efficiency across the fleet.
The importance of how forklift tires are manufactured
The lifespan of a construction tire isn’t just tied to tread design. Rather, it’s shaped by the compounding process used to blend raw rubber and additives. Two methods dominate: dry mixing and liquid mixing, each with distinct impacts on durability, traction, and performance.
Dry mixing mechanically combines solid rubber polymers with powdered additives like carbon black and silica under high heat and shear forces. This creates a dense, abrasion-resistant compound ideal for heavy loads and rugged terrains. However, traditional dry mixing can struggle with uneven dispersion, risking weak spots in the rubber.
Liquid mixing, by contrast, dissolves polymers in solvents before blending additives, achieving flawless consistency for compounds that prioritize flexibility or low rolling resistance.
The future of tire compounding lies in leveraging such technologies to bridge the gap between dry and liquid mixing strengths. They must deliver compounds as tough as they are efficient. That’s where EcoPoint3 technology comes in.
What is EcoPoint3 technology?
A unique liquid-phase mixing process, the patented EcoPoint3 technology enables MAXAM’s high-performance series to take your warehousing operation to the next level in terms of durability, performance, and efficiency. EcoPoint3 is the backbone for the next generation of material handling tires. The process mixes materials evenly, down to the molecular level, creating an even dispersion of the ingredients that go into creating the compounds in your forklift tires, resulting in absolute precision performance and durability.
For decades, specialty tire engineers faced a trade-off: improving heat resistance weakened cut resistance, and vice versa. Our breakthrough technology eliminates this compromise. By reengineering rubber at the molecular level through a novel manufacturing process, we’ve simultaneously enhanced both properties without trade-offs. This leap forward extends tire lifespan in extreme heat and harsh terrains while delivering unmatched durability, thus redefining performance standards for industries where resilience is non-negotiable.
MAXAM Tire carries out its endurance testing through the TÜV Endurance Testing Center in Germany. This state-of-the-art facility, part of a recognized network of accredited tire testing laboratories in the EU, is equipped with advanced technology to rigorously assess tire performance. Renowned for its expertise, the center has been acknowledged as one of the premier independent reference laboratories globally for its precision in measuring rolling resistance, which is a critical factor in tire efficiency and sustainability. Below, see how the EcoPoint3 technology performed in an independent test from TÜV:
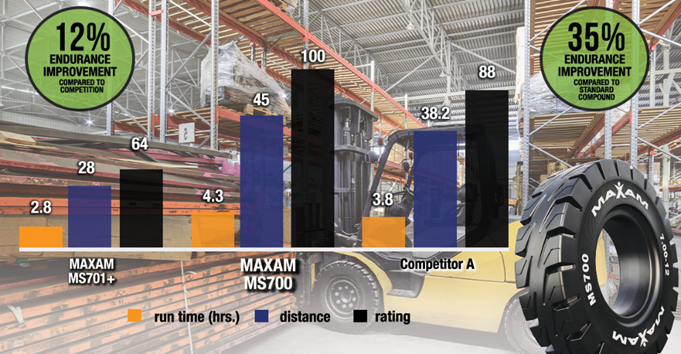
At MAXAM, we’re addressing the pain points of material handlers by reducing costs, enhancing safety, and ensuring tires keep pace with relentless operational demands. The TÜV-validated results make a compelling case for upgrading to tires engineered with cutting-edge compounding technology.
Want to learn more about this technology? Here are other resources: