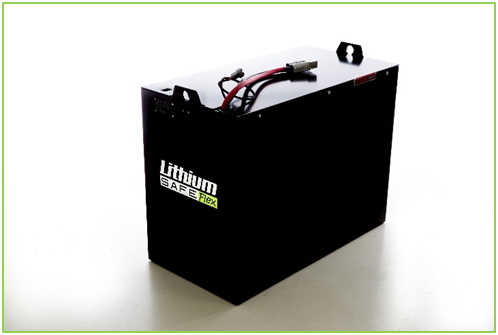 |
There is a new technology in the material handling world, and its name is lithium ion. The days of consistently switching batteries with high maintenance times are over. Lithium ion battery systems offer a relief from all the hassle. While lithium ion batteries may have a larger up-front cost, the ROI is above and beyond any comparison. Traditional lead-acid requires one battery per shift for each piece of equipment where lithium ion only requires one battery per piece of equipment, no matter how many shifts. For lead-acid, this means higher cost and valuable time being spent switching between batteries every shift. Battery switching takes an average of five minutes per shift, if you run three shifts per day, five days per week, for an average of 15 batteries for five pieces of equipment. This is equivalent to losing over an hour of productivity each week! Multiply that number by the size of your fleet and watch the time and productivity loss add up quickly. Lithium ion batteries require absolutely no switching at all, every minute of work is utilized. Lithium ion batteries work at their best when opportunity charging is utilized. This means that during breaks and meals for just short spans of 15-30-minute charges throughout each shift, those will keep the battery running throughout its entire life. Lithium ion battery charging is a very straight forward, a simple process completed in a very short amount of time; the same cannot be said for lead acid batteries.
Each lead acid battery requires an estimated eight hours of charging and eight hours of cool down. During the charging process, explosive gasses accumulate that could lead to some very dangerous situations without the proper ventilation systems. Also, this takes up valuable space in the warehouse that could be used for product storage and the valuable time of employees that could be spent more productively. It takes one employee, sometimes more, to keep all the batteries on proper rotation and to keep the storage room clean. This takes an average of 15 minutes spent per shift, at three shifts a day, 5 days a week for 15 batteries for five pieces of equipment; that is over three hours every single week!
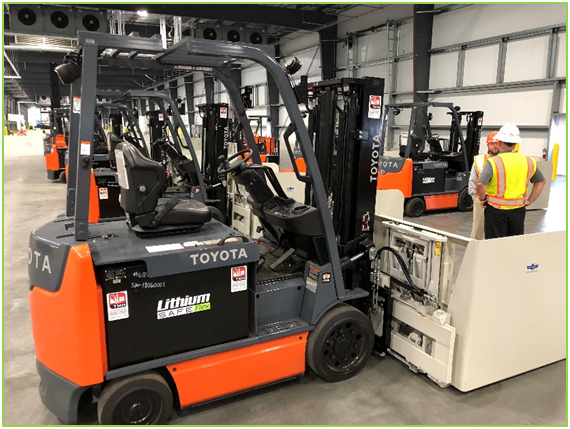 |
Maintenance, repair, and operations (MRO) costs associated with lead acid are very high when compared with lithium ion. Lead acid batteries require weekly, or depending on usage, possibly even daily watering. Cost associated with this includes time spent, water required, watering systems, and personal protective equipment (PPE). Lead acid batteries need periodic cleaning to keep the corrosive acid from damaging the battery, equipment, or an employee. That can equal around an hour a week for a five-piece fleet. There is a delicate balancing act that needs to be closely monitored with every lead acid battery. From the charging to the watering, battery swapping, cleaning, and every task in between, lead acid batteries require an extensive amount of time spent keeping them running properly.
The associated cost with purchasing a lead acid battery adds up quickly and uses valuable floor space. From the cost of the employee's time to maintain each one (watering systems, multiple chargers, PPE's, replacement batteries, and more) the upfront cost of a lithium ion can quickly show value when none of the associated costs of a lead acid battery are needed. When you add in the saved time of all the lead acid related tasks mentioned above, the lithium ion ROI really stands apart. The lead-acid tasks mentioned above add up to a total of six hours a week per 5-piece fleet! For example, if you run a three-shift operation for five days a week with twenty pieces of equipment and multiply that by four, then the operation is losing an entire 24 hours every week with lead acid battery associated tasks. That is a loss of 52 working days a year lost due to maintaining the power storage systems. A fleet with 40 pieces of equipment would be losing 2 days every week and an 80-piece fleet would lose 4 entire days each week. This does not include the employee's pay. Imagine the possibilities of where that time and money could be more wisely spent if you cut out the hassle and make the switch to lithium ion.
Green Cubes Technology is the leading provider of lithium ion battery systems. GCT is an engineering-led company with product manufactured and shipped from the USA. Green Cubes Technology has accrued over 150+ years of lithium battery knowledge across diverse applications. With more than 33 years of developing countless power systems for multiple applications, we understand all the advantages, and we offer systems for all class I, II, and III forklifts and pallet jacks, as well as, AGV's and ground support equipment. Our battery systems are environmentally friendly, sustainable, maintenance free, have optimized performance, and a high efficiency rate, saving time and money across the board.
Contact our sales team today
by email or call +1 (765) 831-8008.
Green Cubes Technology Corporation4124 Cartwright Drive, Kokomo, IN USA 46902
Tel: +1 (765) 831-8008
Email: send an emailWeb: www.greencubestech.com