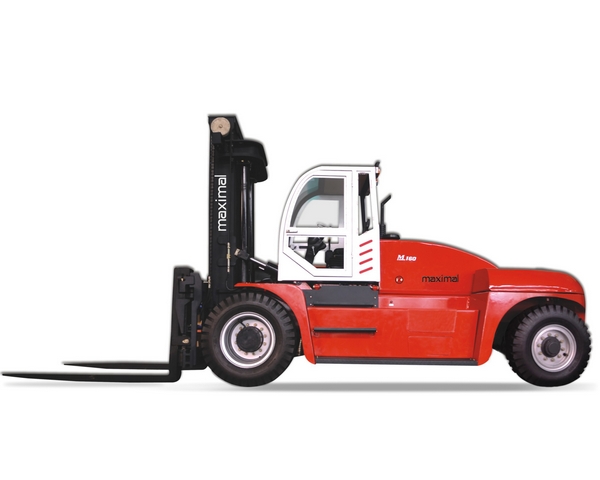 Maximal's 16T and 30T diesel forklift |
There is an increasing trend in the logistics and intermodal sectors to lift ever heavier loads.
Melissa Barnett looks at how the materials handling industry deals with the technical, logistical and safety aspects of lifting heavy loads at a time when everyone wants both speed and efficiency.
When the materials handling industry talks about a "heavy load", they tend to talk in double figures - 8 T to over 50 T. Cascade Corporation considers loads that cannot be palletised and those greater than 8 T as heavy. Herman Klaus, director of application solutions for Hyster big trucks, explains that loads over 9 T means applications are more specialised and the forklift becomes an integral part of the overall operation. Kurt Barbier, sales manager for Belgian attachment manufacturer Little Giant, says anything above 16 T with a 600 mm load centre is heavy. Johan Hellström, product manager for Kalmar, says if the load is over 40 T, is not a container and is bulky, difficult to handle and control, then the load is considered heavy. At this point, he adds, the load often requires specialised lifting attachments or forks.
US manufacturer Hoist Forklifts starts production at 8 T and regularly manufactures forklifts of up to 47 T. Jentry Prine, spokesman for Hoist, says that manufacturers of heavy forklifts must manage the technical challenges of heavy lifting without the machines becoming so large that they become cumbersome, difficult to operate and compromise safety. Hoist uses higher grade steel to minimise the overall forklift size and engineers the equipment so that the hydraulic components on a 50 T forklift are sized so that the 'feel' is no different to a 5 T forklift.
Nicholas Bell, managing director of UK attachment manufacturer MSI Forks says from 10T upwards is considered heavy, with attachments at this level requiring a high level of expertise and technology due to the extreme working environments in which the equipment often operates.
It appears that weight is not the only factor in deciding if a load is heavy. Gregory Mann, business development manager for Australian straddle carrier manufacturer Isoloader, suggests that a heavy load also involves consideration of overall size and complexity of the lift. Janina Weigel, marketing manager for German forklift manufacturer SANY, explains that heavy loads can be interpreted in many ways: "In our industry sector, we would say from 16 T is a heavy load because the way the load is handled gets more dangerous and needs close attention from more than one person when handled." SANY is currently customising a 60 T reach stacker to handle windmills. The forklift will be equipped with a crane hook to lift the weight and awkward dimensions of the windmills and negotiate how the load must be lifted.
Keeping steadyStability, visibility, manoeuvrability and speed are the catch cries for heavy load lifting. These are largely determined by the type of load being handled, the surface conditions and the space in which the forklift is operating. It appears that many of the current working environments are less than ideal for heavy lift operations - a challenging problem for both manufacturers and dealers. Richard Rich, wholesale manager for USA forklift dealer H&K Equipment, says that the biggest obstacles to heavy load lifting are the terrain and the surrounding facility. He explains, "Many plants were built years ago when the loads topped out at 9 T; now it's 45 T. You need a much bigger machine to handle that, but the plants aren't always accommodating. You're restricted by the layout and by openings to get in and out. It's always been a problem, but it's getting worse."
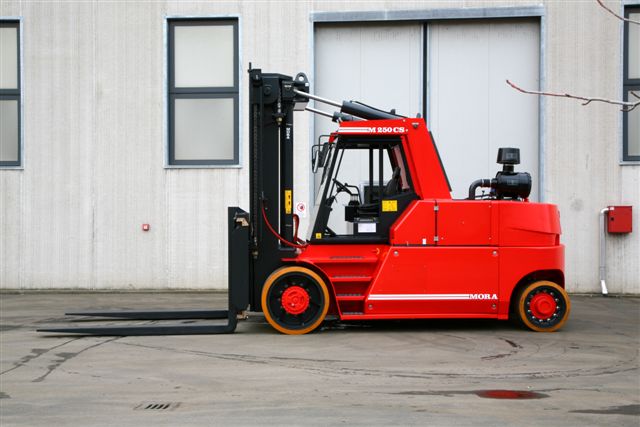 MORA model M 250 CS |
Cees Halling, region sales manager for Dutch dealership BS Forklifts, says it is a similar story in Europe. "We are seeing more 'problem cases' and our sales team is becoming specialised in calculating capacity and load centres, working areas and, most importantly, dealing with unexpected circumstances - low passages, dangerous production methods, etc. It is very important to visit the working area to be able to suggest the correct forklift." For example, at a logistics centre in a large Dutch steelworks, where space was limited due to large end-products and small warehouse space, a Mora 25T M250CS with a length of just 4.45 m and a width of 2.2 m was suggested.
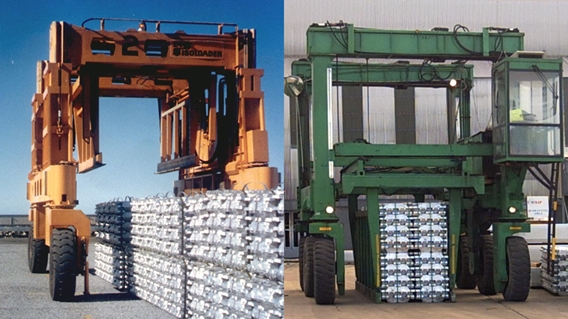 Isoloader straddle carrier lifting ingots |
Heavy loads are usually large and often bulky, so physical size poses a number of challenges including load and truck stability. Mann agrees that stability is a key concern with many heavy lifts and that one of the advantages of using straddle carriers is that the weight can be evenly distributed, sometimes over more than one machine. "Using tandem machines provides even lighter load distribution over more wheels and provides very good manoeuvrability often critical in tight access or confined work sites," he explains. A good example of this system in use was Isoloader's contract to handle 35 m,
70 T concrete girders on an open project site with unsealed surfaces. Two straddles operated in tandem at each end of the load, ensuring traction and manoeuvrability in all conditions.
Tom Schults, managing director for Australian manufacturer Mobicon Systems, adds, "When a forklift lifts a heavy load, almost all the weight is on the front axle. This means that a forklift carrying a 35 T container will have an axle load of around 75 T.
Many surfaces cannot handle this load and damage to the yard surface occurs, exacerbating the problem between an uneven surface and forklift stability."
According to Mobicon, its products have the lowest wheel weight in the world and, being a straddle carrier, can work on imperfect ground - including light concrete - without destroying it.
Tipping is an ever-constant concern when lifting extremely heavy loads. To ensure full stability in SANY's forklifts, it has implemented anti-tipping sensors throughout the forklift to avoid overloading. In the case of reach stackers, there are two anti-tipping devices. The first works through the hydraulics, sensing pressure fluctuations. The second is a sensor which continuously measures pressure in the rear axle. Whenever the pressure goes beyond a point, the operator is alerted to a potential tipping event.
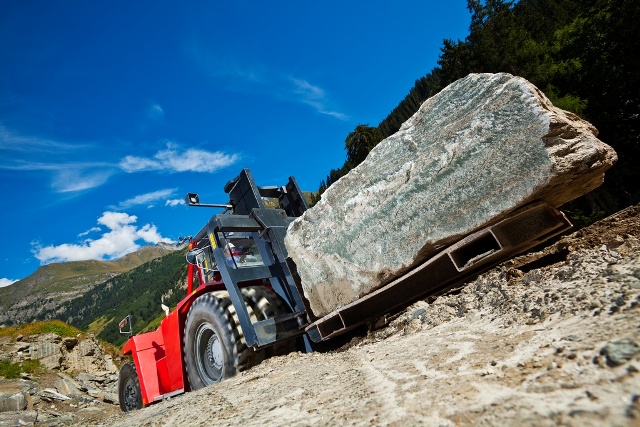 Kalmar DCF500-12 lifting at a Swiss quarry |
Hellström agrees that one of the main technical challenges is to have tyres and drive axles that can support the extreme loads that heavy lifting creates, but he believes that the mast and forks on a forklift also come under enormous stress. In 2012, Kalmar delivered a DCF500-12 to a stone quarry in the Swiss Alps. The forklift had a lift capacity of 50 T at a load centre of 1,200 mm. It was used to handle huge stone blocks over uneven terrain with steep slopes in muddy conditions. Kalmar addressed the issues that the site and application posed by using high-strength steel for mast and forks and appropriate lift attachments.
Heavier lifts, heavier costsHeavy lift forklifts are expensive to purchase and their operating costs are far greater than smaller forklifts; therefore, it is crucial to keep operating costs under control. Two of the main costs are fuel and tyres. Despite the high fuel toll lifting a heavy load imposes (a loaded container handler may consume 10-20 l of diesel per hour, depending on its duty cycle) and increasingly restrictive emission control regulations, there are few alternative energy options currently available to heavy lift forklifts. Hyster's Klaus believes that although alternative energies and hybrids will have a place in heavy load forklift operations in the future, it will be some time before the economics work for customers. However, if anything is going to drive this change sooner, it may be the port facilities, with a number of ports including Los Angeles establishing "green initiatives" and investigating the use of big trucks in electric configurations.
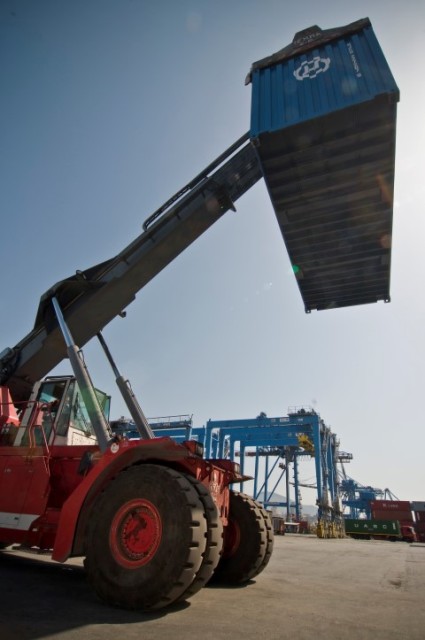 Marangoni retread tyre for industrial equipment |
Tyres are another substantial operating cost. Klaus explains, "Tyres on heavy load forklifts are large and expensive, often more than USD4,000 per tyre, with six tyres per truck. In a normal heavy lifting environment, tyre costs can exceed USD5 per hour of operation and some applications may cause extensive tyre damage, resulting in even higher costs." Giovanni De Bei, marketing manager for Marangoni, agrees and adds that the average performance of a heavy load forklift can be as low as 2,000 hours due to the severity of their applications, heavier loads, higher speeds, runway lengths, site conditions, driver experience and, of course, tyre management. Luca Mai, executive sales manager for the company's earthmover division, suggests tyres which have low heat generation and resistance to abrasion and sideways stress work best in heavy lift situations - such as Marangoni's MRL and MS-IND profiles, specifically designed for retreading straddle carriers and reach stackers.
Other challengesSafety is one of the biggest challenges facing heavy lift forklifts and often it is reduced visibility which compromises safety. Visibility is reduced quite simply because the load is so much bigger in physical size that it tends to obstruct the driver's all-round view. For example, when moving oversized paper rolls, Italian attachment manufacturer Bolzoni's paper roll clamp can be raised or lowered along the vertical load to improve visibility around it. Many heavy lift manufacturers address reduced visibility by adding cameras to the machines. Weigel explains that SANY offers a 360° camera system which enables the driver to have full visibility. Hellström says that Kalmar also uses cameras which can be placed in the mast, counterweight or in the attachments to give a full view of the surroundings. Visibility can also be improved, adds Hellström, through cabin design (using cabins with larger, curved windows), cabin placement or by raising or lowering the cabin around the load. Another option is a turntable seat which is electronically controlled and will rotate the whole driver space in just a couple of seconds.
Matching attachment to lift requirement is vital and sometimes challenging in heavy lift applications. Bell of MSI explains " It is often the case that the pocket size a fork attachment is required to fit into does not get larger as capacity increases, this means that fork attachments for heavy lifts need special steel alloys and advanced forging and heat treatment to meet the forklift's lifting requirements. Forklift arms are often virtually hand-made to suit a heavy lift application.
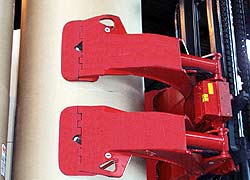 A Bolzoni Auramo paper roll clamp. |
Experience, says H&K's Rich, is the difference between safe and unsafe heavy load lifting. "The job becomes more dangerous when you introduce very heavy loads," he explains, "and we find it's often experience that makes the difference. In the past, operators grew in their careers alongside each new series of heavy forklift, but these guys have since retired or moved up. A new relatively inexperienced generation is replacing them and being asked to lift larger loads than anyone has ever had to deal with before. This inexperience has become a major problem and we've seen an increase in customers asking us for more intensive training of the younger operators - it is a trend that I think is going to grow."
The biggest challenge 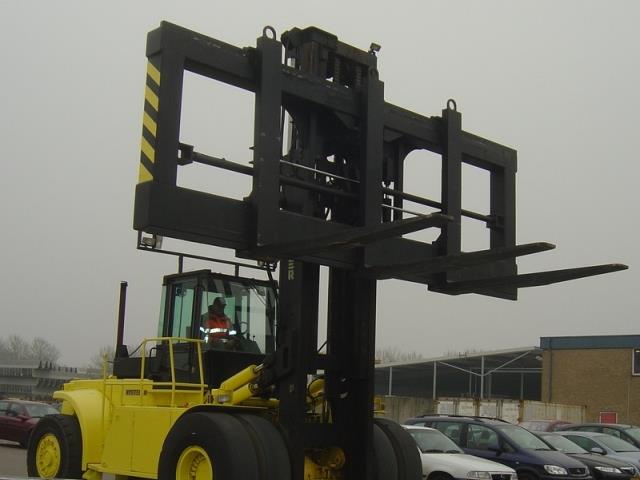 Little Giant container handling attachment |
You cannot talk about heavy load lifting without some mention of the unique challenges in that most taxing of forklift environments - the port terminal. Reach stackers and container handlers make up some of the heaviest load lifters in the sector and both are found at ports and their storage facilities. Ports are challenging both in their physical working environment and in their logistics.
Salty, muddy roadways at ports, often with pot-holes from excessive use at ports require a robust machine. "It is not only the constant flow of materials handling and the need for durability but the extra protection and engineering required for weather, sand, mud and salt on attachments and forklifts which is the challenge," Barbier explains. "These environments are brutal if the forklift operator doesn't understand general safety instructions for loading."
Mann agrees that port sites are often corrosive environments and says that attention to detail on cabs, such as IP ratings of penetration, gaskets and enclosures, not only provides operators with superior comfort, but also prevents premature degradation of control systems.
Cascade's spokesman says that one of the unique challenges when designing products for use in ports is to engineer an attachment that can both handle the large capacity and be durable.
With shipping containers, he explains, the challenge is height, travel distances, movement volumes and environmental concerns. With bulk freight, it is having the correct equipment on call to handle the vast array of loads that come through the port, such as designing a high capacity pulp bale clamp that can move 64 bales of pulp at a weight of 18,000 kg at once.
Klaus agrees that there are some special requirements at ports and terminals. The growth in trade and containerisation, he believes, has exceeded investment and expansion at ports, forcing them to higher density storage and higher stacking. In addition, the high level of traffic plus the big ships often contribute to high levels of pollution, so low-emission engines are important.
The waterfront is a 24/7 economy, which asks a lot of endurance from the people and equipment that work there. Minimising downtime through reliability and ready access to parts is vital. Marcel Vanden Top, general manger for parts supplier Intella Lift Parts, says that ports customers are most interested in top quality spare parts with 24 hour availability. "They simply can't afford for one of their pieces of equipment to be down," he says. If the equipment is out of action, the containers don't get moved, another ship comes in, and the whole system gets backed up. He adds that many terminals are global organisations that demand global supply arrangements - they don't want to pay one price on one continent for a spare part, and then another price on another continent.
And did we mention size? Kalmar recently entered the record books thanks to the heavy lift capabilities of its latest reachstacker, named Super Gloria. The reachstacker lifted a steel component weighing over 100 T in September 2014 at Kalmar's multi-assembly unit in Lidhult, Sweden.
The new DRG1000-92 ZXS reachstacker is the world's largest industrial reachstacker in Kalmar's Gloria range. It boasts a completely new design, developed to meet a customer's specifications with lift capacities up to 120 T.
Additional information by our contributors: HEAVY DUTY APPLICATIONS
Little Giant Europa NV:
website------------------------------------
HEAVY METAL AT ITS BEST: BIGFORKS MADE BY VETTER
VETTER Umformtechnik GmbH:
website,
ShopFront------------------------------------
THE HIDDEN COST OF THE WRONG CHOICE
Mobicon Systems:
website------------------------------------
BOLZONI AURAMO SOLUTIONS FOR HEAVY DUTY FOREST PRODUCT HANDLING
BOLZONI S.p.A.:
website,
ShopFront------------------------------------
HEAVY, LONG OR BULKY INDUSTRIAL LOADS? ISOLOADER HAS YOU COVERED
Isoloader:
website,
ShopFront------------------------------------
PARTS FOR BIG FORKLIFTS - VANGENT AND INTELLA: GLOBAL SUPPLIERS OF FORKLIFT PARTS
Intella Liftparts Inc and VanGent Forklift Parts:
website------------------------------------
MSI-Forks Ltd.:
website,
ShopFront------------------------------------
RELIABLE DELIVERY OF QUALITY USED FORKLIFTS AND CONTAINER HANDLERS
BS Forklifts International BV:
website,
ShopFront------------------------------------
FORKLIFT SCALES: JUST WEIGH THEN GO
Cascade Corporation:
website,
ShopFront------------------------------------
SOURCING LIFT TRUCKS FOR HIGH CAPACITY AND UNIQUE APPLICATIONS
H&K Equipment:
website,
ShopFront------------------------------------
FIRST SANY REACH STACKER ARRIVES IN SWEDEN
Sany Germany GmbH:
website,
------------------------------------
HEAVY DUTY, HIGH QUALITY THAT'S HOIST
Hoist Liftruck Mfg. Inc.:
website,
ShopFront------------------------------------
MARANGONI MARIX TYRES: RELIABILITY, SAFETY AND PERFORMANCE
Marangoni S.p.A.:
website------------------------------------
NEW ELECTRIC FORKLIFT TRUCK FOR HEAVYWEIGHT INDUSTRIAL APPLICATIONS
Kalmar Forklift Trucks:
website,
ShopFront------------------------------------
LOAD HANDLING IN THE HARSHEST PORT OPERATING ENVIRONMENTS
Hyster Europe:
website------------------------------------
KAUP-ATTACHMENTS IN 'HEAVY LOAD-VERSION'
KAUP GmbH & Co. KG:
website,
ShopFront------------------------------------
Zhejiang Maximal Forklift Co., Ltd.:
website,
ShopFront