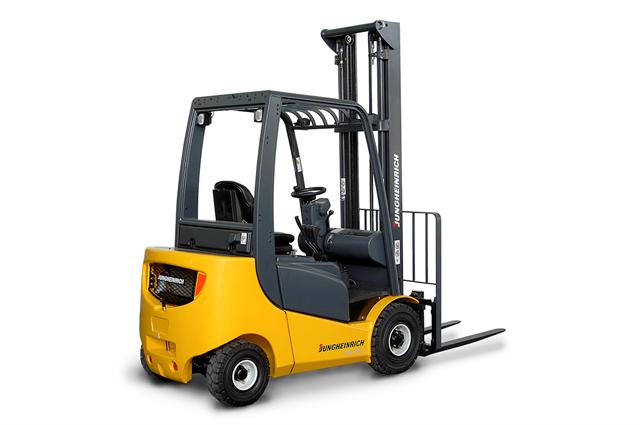 Sharpak has replaced its old forklifts with a fleet of Jungheinrich's EFG Series trucks. |
Sharpak, part of Groupe Guillin and a UK manufacturer of rigid plastic packaging, has replaced its old forklifts with Jungheinrich's EFG Series counterbalance, powered pallet and reach trucks fitted with the manufacturer's SnapFit battery-changing mechanism.
"It is never easy to say 'goodbye' to a long-term supplier, but we are delighted that we made the change to Jungheinrich," says Karl Traynor, Sharpak Yate's logistics manager. "Our lift truck operators find the trucks more comfortable and the controls more responsive."
Because it serves the food sector, Sharpak has to adhere to strict hygiene regulations and so all the materials handling equipment employed at the site is electric-powered.
Battery changing and recharging takes place in a dedicated area of the building, but during a routine battery swap, an experienced forklift operator managed to spill the battery she was removing from a counterbalance truck onto the floor.
Sharpak says the subsequent battery acid clean-up process was costly and disruptive to the company's intralogistics processes. The mishap occurred several months before its existing and longstanding contract with a forklift manufacturer ended.
The company decided to seek a forklift provider that could offer a system capable of avoiding any chance of a repeat of the accident. "Our forklift supplier at the time of the accident - who had been our supplier for some 20 years - shrugged the event off as human error," Traynor explains.
"Of course, people are responsible for 99.9% of all accidents, but we wanted to see if there was something available that minimised the likelihood of the same thing happening again," he says.
Several million plastic trays are produced each day at the Yate, Gloucestershire facility for a range of customers in the food-processing sector. The factory and finished goods warehouse sit side-by-side on the same site, and materials handling equipment is used to undertake a wide range of tasks.
At the factory side of the building, counterbalance trucks unload incoming raw materials, which can be palletised or delivered in bulk bags. On the other side of the dividing wall, which separates the factory from the finished goods store, counterbalance and powered pallet trucks deliver palletised loads to the racking, collate orders in the loading bay marshaling area and load outgoing delivery wagons in the yard.
The SnapFit device locks to the underside of a 48 or 80 volt battery to allow the battery to be removed easily, quickly and safely. "The SnapFit system is a simple but highly effective piece of design that is not only safe but also speeds up the battery-changing process," Traynor says.
"I now have regular meetings with my contact at Jungheinrich at which we discuss any issues that may arise to ensure that our needs are being met by the trucks. This is so different from my relationship with our previous supplier who I only saw when our contract was due for renewal."