Principally focused on the wire and cable, and pipe manufacturing, Borealis in Sweden supports customers with speciality plastics for some of the largest energy supply, oil and water pipeline projects in the world. Rocla's automated guided vehicles (AGV) have been working constantly at this unique site for over a decade now transporting special containers. Rocla's automation solution has enabled Borealis to increase the storage space and speed up the flow of work while minimizing the damages. 14 Rocla AGVs carry over 15 000 octabins Borealis was formed in 1994 with the merging of Neste and Statoil. With more than 50 years of experience in polyolefins and using unique Borstar
® technology, Borealis focuses on providing plastic materials to the infrastructure, automotive and advanced packaging markets across Europe, the Middle East and Asia. Company is a leading provider of chemical and plastics solutions and committed to the principles of Responsible Care
®.
In 2001
Rocla received an order from Borealis which consisted of 10 AGVs. In 2003 Borealis added 4 new AGVs to the existing system. The 14 Rocla AGVs are transporting octabins from production to the storage and from the storage to dispatch area for lorries. An octabin is a special container - it is an eight edged cardboard cylinder placed on a pallet, approximately 1100x1100x1800 mm with a weight of 800 kg. The octabin is filled with polyethylene granulate. The storage is a buffer store for different production batches. There are two different parts in the storage: the largest part contains normal catalytic processed polyethylene and the smaller part for PEX, the super clean polyethylene. PEX needs to be stored in normal temperature so this part of the storage is heated wintertime.
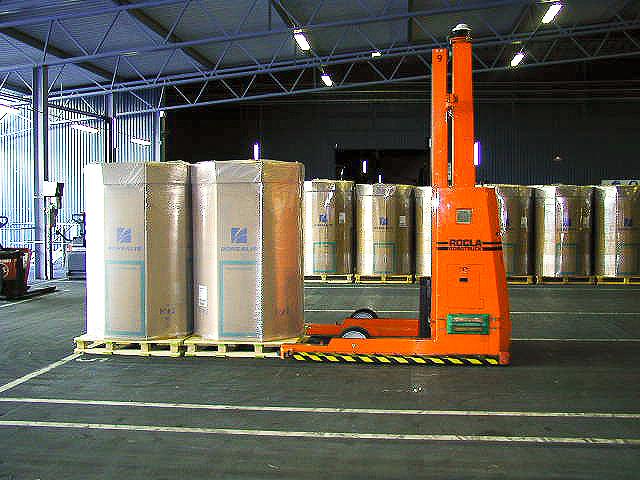 |
The total warehouse area on site covers 24 700 square meters and contains 15 231 octabin pallets. The turnover factor is eight times a year. The flow has stayed constant during the eleven years of automation. In the storage lanes these octabins are standing two by two, on top of each other to get a factor two of storage capacity.
The automated transport system provided by
Rocla could run 24/7 continuously, but at the moment it works 18 hours a day, 7 days a week, in both dispatch and filling the warehouse. The storage is automatically rearranged: When a stored batch in four lanes has been partly consumed, if there is a possibility to compress it in to two lanes a rearranging routine will start.
Special for Borealis is the load-on-load with height searching application: The polyethylenes granulate will compress during the time, especially since the second pallet on top presses the one below with its weight. For this reason the AGVs are searching the pallet tunnels with their sensors in the fork tips.
Why Borealis chose automation? "Reducing the damages and mistakes on site were the main reasons for choosing automation. With Rocla's automation solution the storage is always correct and up-to-date. The AGVs are pre-programmed, which also means the system will tell directly if there is something wrong. The rearranging in the warehouse is made without people and can also be made during the night. Since one pallet has a value of an average monthly salary and the cleaning of the tiny plastic pieces takes a lot of time, reducing the damages was truly a top priority for us," explains Peter Nykvist, Logistics Material Handling Maintenance Service Engineer at Borealis.
Excellent experience with measurable benefits with Rocla's AGV system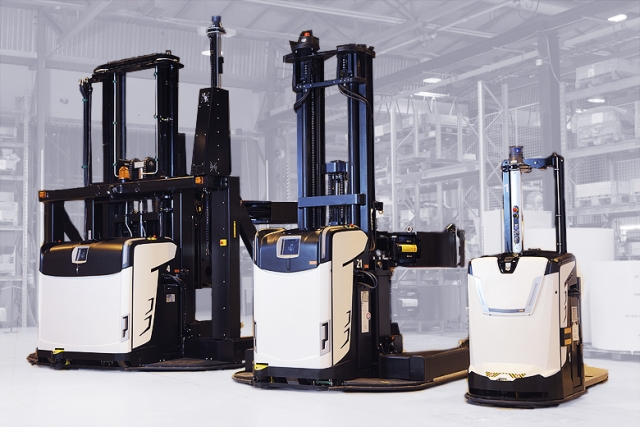 Today Rocla offers full line of modular AGVs for different customer applications. |
The first delivery with 10 vehicles was implemented more than a decade ago. It was acquired to solve the customer's need for more storage space in one location. Before Borealis used to rent storage spaces in different locations, which resulted in logistic problems, like keeping different stores in order and shipping from different batches located in different stores. The rearranging of the consumed batches compressed the storage and saved a lot of space. Borealis could store and dispatch in one location with the help of Rocla's automation solution.
Earlier more damages took place in several storage locations. The octabins had to be moved and transported by lorries from location to another, which was both time consuming and meant extra transportation costs. Each load handling phase added more possibilities for damages and required more work force. The current automation solution not only reduced damages but also cut down labor and transportation costs while making the logistics process more efficient and saving time.
During these years of operation
Rocla's AGV system has been developed further and updated technologically. The latest tasks were to increase the out feed speed and to increase the available storage space. The available storage has been increased by reducing the distance between the octabins in the lanes and also by using those square inches that were blocked by pillars earlier. All these actions had to be implemented carefully step-by-step because of the complexity of the storage. These efforts have really paid off: the transport efficiency has increased over 50% and the storage has increased with 1000 extra locations.
The Borealis facility has been extremely popular to visit during these years. Both possible customers and students have visited the site to see this unique AGV application and the improvements in the working environment. Borealis plans to use this well-functioning system also for the next ten years.
For more information on Rocla's comprehensive AGV solutions please visit www.rocla.com/productlist.asp?Section=477
ROCLA OY
Email: agv@rocla.com
Web: www.rocla.com
AGV Sales: +358 20 7781 332
AGV Services: +358 20 7781 312
P.O.Box 88
04401 Järvenpää
FINLAND