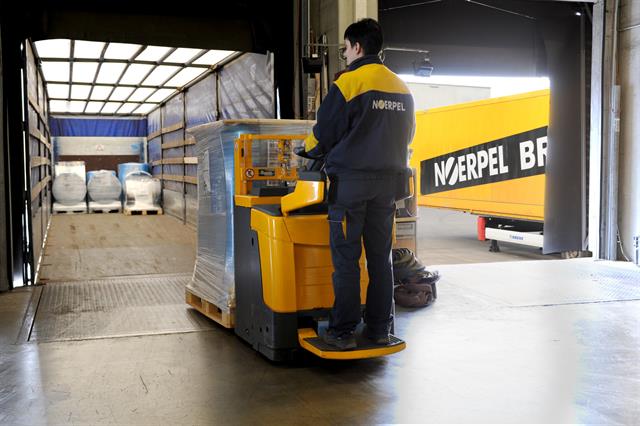 Jungheinrich's after-sales programs includes web-based products like its Information System for Stacker Management (ISM) Online. |
Fleet management services are an important revenue source for truck manufacturers. As AUSA launches what it calls an "innovative after-sales concept" this year, other forklift manufacturers
Forkliftaction.com News contacted say their after-sales programs are also using the latest technologies and offering customers the best service.
Last month, Spanish rough-terrain forklift specialist AUSA introduced an after-sales program for its German customers, developed by Roger Tornero who was responsible for the spare parts and after-sales department in the Volkswagen Audi Group in Spain.
The new program that offers a "total solution" to AUSA customers was designed in 2014. Tornero says the new after-sales concept uses the latest technologies, is based on new Web 3.0 technology and is a total breakthrough compared to AUSA's previous model.
"In relation to after-sales, this new approach means that the machines are constantly sending information to our HQ, allowing us to monitor a machine, and allowing us to know if the machine will need a maintenance service or if the machine is likely to suffer a breakdown."
This flow of information allows users to know what will happen in the near future and take corrective actions, he explains. It represents a change from a reactive approach to a proactive one, shortening the reaction times, decreasing downtimes and cost of ownership, as well as increasing customer satisfaction.
AUSA declines to reveal the details of the technologies used for its new after-sales program.
Leading German forklift manufacturer Linde Material Handling GmbH says it is already using "all relevant and modern technologies" for its after-sales programs. The company agrees that preventative maintenance is essential to optimise service performance.
Spokeswoman Heike Oder says the recently relaunched fleet management solution, Linde connect:, offers several functions to help customers to proactively manage the maintenance of their fleet, regardless of truck brand. Customers can use connect: to monitor the entire fleet and get automatic reminders of pending service intervals; trucks that are heavily used or suffer continuous shocks can be identified and looked after before serious damage is done.
"The Linde standard for fleet management via the locally installed fleet management software, connect:desk, is Bluetooth, which is very reliable and resistant to interference.
"For the decentralised Linde online platform, connect:portal, the GPRS mobile radio standard is used, which is available worldwide. This solution is also open to customers who want to access their fleet data wherever they are and also via mobile devices like smartphones or tablets. The data transmission hardware as well as other connect:hardware components can be retrofitted to older Linde trucks as well as to trucks from other brands."
Oder adds that Linde continues to develop new hardware functions that help monitor the performance of a truck, for example, the truck's battery management.
Linde is currently looking into the automation of the whole process of transmitting error codes from the truck, ordering spare parts, scheduling the service technicians and keeping customers continuously informed about the status of a service job.
Together with Frankfurt-based IT services company, T-Systems, Linde says it is setting up a test project involving an app that provides customer and service technician with all of the relevant information.
Another leading German forklift player, Jungheinrich AG, says its after-sales programs are definitely proactive in nature.
Spokesman Jan Kaulfuhs-Berger explains: "Jungheinrich is active in defining and working on the market and the target groups. We develop frequently new services to create additional benefit for our customers."
Kaulfuhs-Berger lists the technologies Jungheinrich uses for its after-sales programs as web-based services like service call via apps, web-based products like Information System for Stacker Management (ISM) Online and the digitalisation of service delivery, for example, the digital signature of service engineers.
Jungheinrich presented the latest version of its ISM Online to an international audience at CeMAT 2014 in Hanover, Germany. The company claims the new fleet management system can manage, analyse and optimise industrial truck fleets, irrespective of their size or complexity. A new feature consisting of the Productivity module allows the user to analyse and consequently maximise the utilisation of the fleet capacity. "This also allows [the user] to introduce productivity control measures for [the] industrial truck fleet at several locations - even internationally," explains André Friedrich, head of after-sales service co-ordination at Jungheinrich.
Kaulfuhs-Berger predicts that the digitalisation of service delivery will become "more and more advanced in future" with the integration of systems and forklifts, remote service and the creation of more digital products.
"Knowledge management will be the recipe for success for the after-sales service," Kaulfuhs-Berger adds.
Paul Watson, UK general sales manager for Doosan Industrial Vehicle (DIV), says that with the company's dedicated dealership network, its after-sales program is "more proactive in approach than other manufacturers".
"Equipped with laptops and iPads for fault diagnosis and to check parts availability and place orders immediately, and with a focus on service and maintenance, our dealers are far more interested and better placed to anticipate and meet customers' needs than other manufacturers."
Watson says DIV works with UK firm Fork Truck Control, and for the first time, has just fitted a Wi-Fi GPS system to a new fleet of trucks supplied to sustainable wood provider Metsa Wood. "This system can monitor and feed back information on performance and servicing needs, [and] also track trucks around the site, so optimum routes can be planned resulting in smarter working.
"The system also includes impact damage detection, so any forklift impacts can be recorded; and if an impact is detected above a specific threshold, the truck halts instantly, preventing any further damage to the vehicle or potential harm to the operator. At the same time, the system sends a real-time incident alert by email to the shift manager and service provider."
Antonio Martínez, managing director of Bomaq Industries SL of Murcia, Spain, a company established in 2013 to manufacture rough-terrain forklifts, tells Forkliftaction.com News Bomaq machines are set up differently to other machines.
"Our after-sales is not proactive," Martínez says. "We don't spend money and resources ... warning or predicting problems, as from our point of view, this does not add value to the product.
"We focus on not having problems, rather than warning about them; this is the heart of our product design and philosophy. We use the best components known, with simple and easy access and maintenance, and where we think a problem can appear, double the system or raise the security factor."
Martínez cites the installation of two switches levers for its forklifts' forward and reverse functions as an example: "The downtime due to a fault of such [a] small component costs much more than the component itself. On the other hand, our market does not like electronics in our product, so they do not depend on computers or fault-detection software. Our product is simple and easy to use, and once you know one Bomaq model, you know all of them."
He adds: "Systems for monitoring the machine status in real time are very useful, but need a base station that controls the parameters and [makes decisions on] what to do.
"We prefer to leave that decision to the driver, who knows all the parameters of the situation, and what the machine is doing in that moment. For that aim, our units are equipped as serial equipment with (a) temperature gauge for hydraulic oil, (a) temperature gauge for engine coolant, lights warning indicators for all the filters installed, and lights warning for other systems like engine oil pressure, battery charge ... all of this without using electronics or complex radio monitoring systems."
What do you think of the latest technologies used in fleet management services? Continue the discussion in
Forkliftaction.com's Discussion Forums.