Tyres and wheels are the only piece of equipment on a forklift in constant and direct contact with the ground.
Melissa Barnett reports that while these components are crucial to the safety, efficiency and handling of the vehicle, they are often the most neglected piece of materials handling equipment.
Clive Green, vice chairman of the Industrial Tyre Association (ITA) in the UK, suggests companies need to treat the purchasing of tyres as an investment rather than as a cost and adds that the most important aspect when choosing tyres or wheels is selecting the correct tyre for both the machine and the application.
Len Sambrook, chairman of the ITA, explains: "Tyres are such an integral part of a forklift or industrial truck that by taking responsibility and following strict standards of specification and fitting of tyres, users can significantly reduce the lifetime cost of the machine. Having the right tyre reduces accidents, breakdowns and maintenance, resulting in cost savings in the long run."
Jean-Paul Mindermann, chief executive of OEM supplier Watt's Tyres, concurs that "choosing a tyre specified according to use, load and environment must be ensured as this is often where end-users get seduced by price rather than value".
Tyre associations, manufacturers and suppliers all agree that if best practices are maintained, then safety, machine longevity and efficiency standards can readily be met.
Choosing the right tyre or wheelBut how to choose the right tyre in a market saturated with choice? Knowing the type of tyre best suited to your machine, application and environment is fundamental. The ITA and a number of tyre manufacturers supply comprehensive tables matching correct tyre to machine.
In brief, solid tyres (also called puncture-proof tyres), cushion tyres and the different varieties of pneumatic tyres are best suited to reach stackers, container handlers, rough terrain forklifts and heavier load-carrying forklifts.
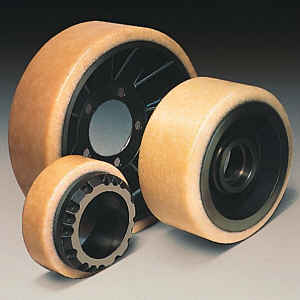 Tractothan wheels by Raeder-Vogel |
Polyurethane, urethane and press-on tyres are used mainly in warehousing applications on narrow aisle and very narrow aisle vehicles and smaller capacity forklifts working indoors. Polyurethane tyres are often produced as a single unit of both tyre and wheel. Polyurethane tyres are also used in applications where rubber tyres just aren't resilient enough, such as in working environments of extreme heat or cold or in warehouse applications moving heavy loads over sustained periods of time.
Other features such as tread, side-wall protection, marking or non-marking options, static or non-static should also be considered.
What is in a tyre?What makes the difference between tyres is their construction and design. This is what ultimately dictates their use and working environment.
Solid or pneumatic industrial tyres are mainly constructed of rubber, extruded and pressed into usually three layers. Between the rubber layers are added layers of reinforcing fabric and bands of high-tensile steel.
The layers are wrapped around a tyre-building drum, then cured by applying pressure and heat. Curing bonds the layers together and strengthens the tyre structure. Large industrial tyres can take up to 24 hours to cure.
The chemical ingredients used during compounding, the number and type of components used in construction and tyre tread design all impact on end-use and cost. The chemical compounds used by individual tyre manufacturers can be customised and are often closely guarded secrets.
Polyurethane tyres are made from polymer compounds which are heated, poured into a mould and then left to cure. The mix of polymers used will determine the type of polyurethane created, from soft foam polyurethane to the hard plastic used in forklift tyres and wheel rims. Polyurethane tyres can be press-on band types or moulded around a steel rim.
A number of tyre manufacturers including Watts, Sun-TWS and Solideal produce both rubber-based and polyurethane tyres. However, polyurethane tyres are more often made by specialised companies, such as Thombert and Raeder-Vogel, which together with Bayer pioneered the unique Vulkollan polyurethane compound.
Working componentsTyre compounds are the basic ingredients of a tyre and are a closely held secret by manufacturers. The quality/mix of the rubber or polyurethane compound gives the tyre its strength, resistance to wear and stability. Products like Solideal's Ad-Trak resilient tyre are claimed to have additional stability due to an innovative chemically strengthened rubber.
Many manufacturers are now using compounds with high natural rubber content, claiming that it produces tyres with a longer working life.
Different compounds can also be used to produce non-marking tyres such as Solideal's resilient Mag2 and Watts range of Premia press-on band tyres. Electric conductivity, improved wet grip, better rolling resistance, and heat resistance are all qualities which can be developed in a customised compound.
Tyre tread is a significant feature on all rubber and polyurethane tyres/wheels as it affects tyre longevity, performance and driver comfort. The EU has introduced a directive regulating whole body vibration. Depth, width and an open-tread design such as in the Nokian Forest Rider help reduce vehicle vibration, improving driver comfort and reducing surface degradation.
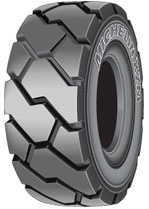 Michelin's radial tyre the Stabil'x |
Tread also impacts on braking ability and stability. Italian tyre producer, Marangoni believes its Eltor 5 series has greater stability due to a deeper grooved and squarer constructed tread. Michelin's Stabil'x tyre has improved stability and driver comfort by reinforcing the tread shoulder.
Much has been made lately of the influence of rolling resistance on vehicle efficiency. Rolling resistance is the friction caused by the surface of the tyres coming into contact with the road surface; the greater the rolling resistance, the more energy needed to move the vehicle, meaning greater fuel consumption and a less efficient and environmentally friendly vehicle.
Lower profile tyres with less intricate tread pattern such as radial tyres have reduced rolling resistance, however grip is compromised with less tread, so application and working environment need to be taken into consideration. A 20-25% reduction of resistance can increase fuel economy by 3 to 5%. If correct tyre pressure is maintained, resistance is further reduced.
Sidewalls on tyres are sometimes the most vulnerable area to puncture, especially on machines working outdoors. Nokian's mining tyres have abrasion protection and extra thick sidewalls. The ForkBoss solid tyre by Airboss boasts uniquely designed oblong sidewall holes which aid in deflection and reduce tread "squirming", resulting in better tread wear and fuel efficiency. The sidewall holes also help dissipate heat faster which contributes to the life of the tyre.
Polyurethane tyres are found in different applications to rubber tyres but often have similar needs for traction, marking and non-marking capabilities, load bearing, stability and conductivity.
Like rubber tyres, polyurethane wheels and tyres have many of these capabilities customised in the compound. Raeder-Vogel has developed Tractothan, a composite material based on Vulkollan but characterised by better traction.
Environmental concerns encourage innovation In the not-so-distant past, the tyre industry was regarded as one of the dirtiest and with good reason. The manufacturing process creates significant waste and uses large quantities of carcinogenic chemicals. Over one billion tyres are discarded a year and, until recently, most of these ended up in landfill or were burned.
Part of the problem has been the difficulty in recycling a tyre. Due to its construction, de-construction was tricky. A typical passenger tyre contains 30 types of synthetic rubber, eight types of natural rubber, eight types of carbon black, steel cord, polyester, nylon, steel bead wire, silica and 40 different kinds of chemicals, waxes, oils and pigments. They typically contain 80% hydrocarbon, 10-15% iron (in the bead wire and steel belts) and a variety of chemical components. The size and robustness of industrial tyres only makes the recycling process more difficult and expensive.
However, over the past five years, with the implementation of EU directives banning tyres from landfill and highly aromatic oils from production and the setting of CO2 emission standards, the industry has been forced to embrace cleaner methods of both production and waste management.
All the manufacturers
Forkliftaction.com News spoke to have implemented environmentally sustainable solutions. Many of them, including Watts, Sun-TWS, and the Finnish recycling company, Suomen Rengaskierratys Oy (owned by a consortium of tyre manufacturers including Nokian, Continental, Michelin, Goodyear and Bridgestone together with the Finnish Tyre Association) have tyre recycling facilities; shredding, crumbing and using the material to create new tyre ranges or diverting it to other products.
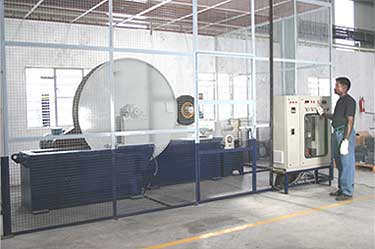 Sun-TWS's iLastic intelligent elastic production control system |
A spokesman for Sun-TWS, a manufacturer based in Chennai, India tells
Forkliftaction.com News that all steam used in the production process at their plant is generated from eco-friendly waste material.
Nokian tyres has completely eliminated high-aromatic (HA) oils in its entire production line. HA oils are classified as carcinogens because they contain polycyclic aromatic hydrocarbons (PAHs). An EU directive has banned their use after 2010. Continental Tyres has also eliminated HAs and nitrosamines from its super-elastic CSEasy range.
Other companies, such as Thombert, utilise less hazardous solvents and compounds or more efficient manufacturing processes to trim waste. Reggie Collette, of American polyurethane wheel manufacturer Thombert explains, "One of our major focuses has been to reduce internal scrap. By reducing waste material off our lines, we send very little now to landfill."
What next for the wheels and tyre industry?The past decade has not been an easy one for the wheel and tyre industry. Having battled rising prices and reduced availability of steel, rubber and iron, as well as the added costs of meeting new environmental standards, the industry now has to deal with the global financial crisis.
For some, this means forging closer ties to their OEMs and developing a more comprehensive idea of their needs and expectations. Mindermann says manufacturers have to respond to the needs of the market. "We have worked closely with OEMs and dealers to understand what products they require and why they need them, and acting exactly in accord with demands".
For others, it means strategic alliances or expansion. Watts Tyre group recently acquired German-based tyre and services business Profix GmbH in a bid to improve services and distribution across northern Germany. Meanwhile, Continental and Gumasol have announced a strategic alliance to produce the Gumasol Softy tyre at Continental's Sri Lankan facility.
Other companies have taken the option to trim staff and production and concentrate on product diversification and improved technology. Forkliftaction.com has been told of one major European wheel manufacturer which has been forced to severely reduce staff and cut production to three days a week to cope with a drop in production units from 25,000 a month to 3,500 in March/April, 2009.
Raeder-Vogel sales director Bernd Dolk agrees that orders from OEMs have been severely cut. His company is facing a loss of orders for the OE business of up to 40%, but on a more optimistic note he adds that "fortunately, due to our widespread customer base, the extensive range of our products and the positive attitude of our trade partners, we expect an overall decline in sales of only 20% for 2009".
Reggie Collette of Thombert, which has also seen a decrease in OEM orders, has the last word: "I believe the market has reached a bottom and will now trend back up slowly. However ... it might be some time before we reach previous levels."