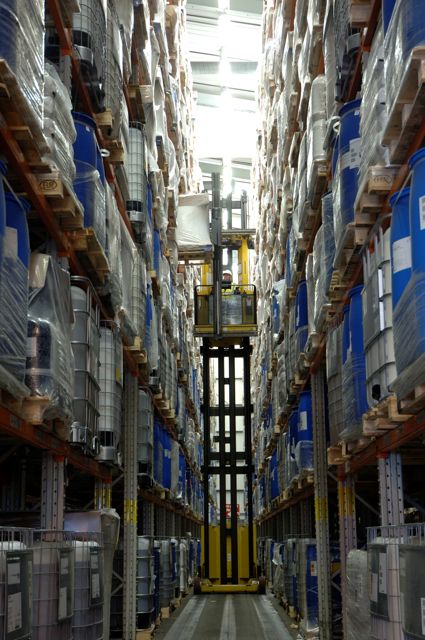 BASF updates the VNA fleet at its Bradford facility. |
The world's largest chemical company, BASF, has increased the very narrow aisle (VNA) Yale MTC fleet at its Bradford facility to efficiently store and handle chemicals.
With racking reaching heights of over 13 m (42 ft.) and 1.65 m (5.4 ft.) aisles, BASF has a very specific materials handling equipment requirement for its raw materials and finished products warehouse, where there are over 25,000 pallet movements each week.
Craig McAllister, BASF's logistics manager at the site, says disruptions in supply can be very costly and can cause the entire operation to shut down. "The chemicals and materials that are stored in the warehouse are required 365 days a year as the site must run continuously ... Our first consideration when replacing the VNA fleet was therefore reliability."
Yale dealer Forkway, working in the UK with Briggs Equipment, secured the deal for the seven VNA trucks and is also responsible for the supply and maintenance of an additional 20 pieces of materials handling equipment on site. The value of the deal is confidential.
Tim Hunter, operations director at Forkway Group, worked with BASF to identify the exact specification of the equipment needed and to recommend a solution that would deliver the performance the company required.
"The solution we provided was based on the best trucks for the specification of the existing warehouse. We identified that the MTC series would offer low cost of ownership, dependability and productivity, combined with operator comfort," Hunter explains.
He adds that as part of the solution, Forkway specified an energy-efficient recharging facility using technologically advanced batteries. "We also included a planned programme of routine maintenance over five years with a dedicated engineer on site to ensure the trucks work to the optimum productivity delivering maximum uptime."
Forkway also boosted warehouse efficiency and reduced downtime by re-specifying the loops used for the wire guidance of the VNA trucks.
Hunter explains: "Previously, the wire laid in the warehouse floor was one continuous loop. This meant that all four trucks could be out of operation if a problem occurred. Now, we have laid eight separate loops allowing the isolation of a specific area of the warehouse should a problem ever occur, leaving the remaining areas unaffected and operating as normal."
The VNA trucks operate using a computerised order picking system that automatically determines the most time and energy efficient route through the racking.
Each 80V MTC15 can handle industrial bulk containers or pallets up to 1.5 T, transporting them from the racking to marshalling areas at the end of every aisle ready for loading and unloading by electric counterbalance forklifts.