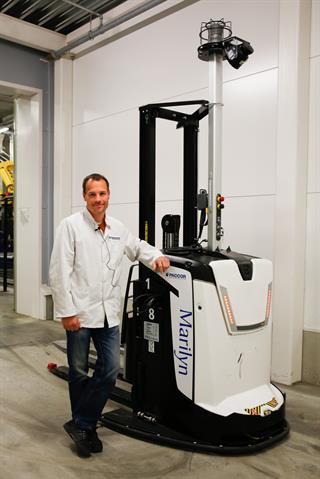 'The process starts with the AGVs picking up cages, pallets and cardboard containers from the warehouse, and taking them to our production area where molding and printing happens.' - Mr. Juhani Karhunen, the Technology Manager, Coveris Rigid Finland. |
The plastics packaging manufacturer Coveris Rigid Finland relies on Rocla's AGV technology. Coveris has a system with six Rocla AGVs (automated guided vehicles) in use at their factory in Finland.The Finnish part of the Coveris was previously known as Paccor. The name change occurred in 2013 when Coveris was formed as five leading packaging companies - Britton Group, Exopack, Kobusch, Paccor and Paragon - joined forces to create the sixth-largest plastics packaging entity in the world. With revenues exceeding 1.8 billion Euros and operations in more than 20 countries, Coveris has 63 factories and 8600 employees both in Europe and North America.
The
AGV system in Hämeenlinna, Finland was delivered to Coveris by
Rocla in 2013. The system consists of six ATX12 automated trucks designed for standard pallet and cage handling and transfer operations.
The AGVs used by Coveris move between the warehouse and production units, and they are able to lift pallets and cages up till 1.8 meters height and handle load-on-load operations. For navigation the
AGVs at Coveris use laser triangulation: reflectors attached to walls, shelves and other structures are scanned by a rotating laser scanner on the truck.
The AGVs handle many kinds of tasksThe AGV system is at use in the new production facilities of Coveris and in the warehouses outsourced to and operated by Itella (Finnish Post). The AGVs perform all kinds of pallet and cage handling operations.
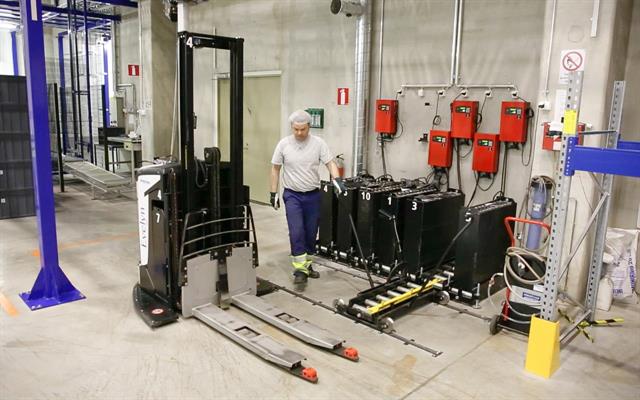 Battery changes happen between orders. When the battery needs to be changed, the truck goes automatically to the changing station where an operator replaces the used battery with a charged one. The process is easy and takes only a few minutes. |
|
"The process starts with the AGVs picking up cages, pallets and cardboard containers from the warehouse, and taking them to our production area where molding and printing happens. The materials also need to be transported between the various production units, and the
AGVs take care of this", explains Mr. Juhani Karhunen, the Technology Manager at Coveris Rigid Finland.
"When everything is ready, the AGVs pick up the pallets and cages from production, usually loading two of them on top of each other. The AGVs then take the load to a stretch wrapping machine and when wrapping is done, the pallets and cages are delivered to the warehouse", continues Juhani Karhunen.
In addition to the automated trucks Coveris has the
Rocla MetRo warehouse management system in use. The MetRo system is also used to control the AGVs' traffic flow, for example by assigning each order to a suitable AGV and taking care of the work queue. When an
AGV is needed for example to take the cages from the printing unit for wrapping, the operator places an order to the
MetRo system and the truck chosen by the system comes to pick up the order. MetRo is tailored to provide all the reports needed, and it is also keeps a record of all the service calls.
Marilyn and Evelyn work in three shiftsAll the AGVs at Coveris are named after women: Marilyn, Evelyn, Patsy, Rita and the rest vehicles move continuously on the corridors of the production facilities and in the warehouse. As the factory works in three shifts, the
AGVs are in use almost all the time, stopping only for shorts periods of time between the orders.
The battery changes happen between the orders. When the battery needs to be changed, the truck goes automatically to the changing station and an operator comes to change the used battery to a fully charged one. The process is easy and the truck is again in use in a few minutes.
"The current AGV system has now been in use for a little more than a year, but we have a long experience of Rocla's automated trucks, as we had a similar system from Rocla at our old facilities. There we had two AGVs, and now have six of them. As we work in three shifts, using
AGVs helps us to cut the material handling costs significantly. It is easy to understand that a similar non-automated transport system would require a lot of people to drive the trucks", explains Juhani Karhunen.
There are a lot of benefits in using AGVs."When routine transportation tasks are automated, substantial cost savings can be reached, employees can be free for more meaningful and productive tasks. Safety on the work floor improves significantly and with AGVs there is also less risk for damage to the products, buildings or machinery", says Mr. Eero Viskari, Sales Manager at Rocla Solutions.
In addition to buying an
AGV system, it is also possible to rent it from Rocla Solutions. Coveris opted for long term rental.
"For many companies rental is the best solution. In this kind of agreement
Rocla also takes care of the service and maintenance of the AGVs so that our customers can fully concentrate on their own business and focus on their core competencies", explains Eero Viskari.
For more information on Rocla's comprehensive AGV solutions please visit www.rocla-agv.comROCLA SOLUTIONS OYEmail: Send a message
Web: www.rocla-agv.comAGV Sales: +358 20 7781 332
AGV Services: +358 20 7781 312
P.O. Box 88,
FI-04401 Järvenpää,
FINLAND
Visit the Rocla ShopFront