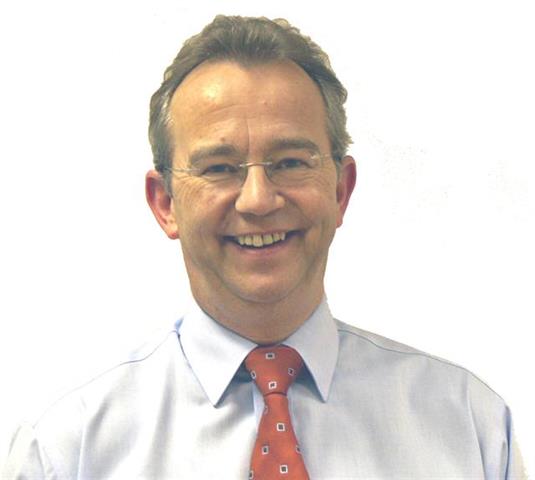 Richard Shore |
Richard Shore is managing director of Mentor FLT Training Limited, the UK's leading provider of training and associated services for all types of materials handling equipment and workplace transport.
The UK economy seems to be gathering pace at last and, understandably, the mood of many businesses seems to be optimism, tinged with caution. Managers are especially drawn to temporary warehouse staff, as casual and agency workers offer extra capacity - fast - to handle increasing workloads, without tying the company into a long-term commitment should business take another dip.
But short-term workers pose special safety risks that can't be ignored. What might seem a low-risk move financially could significantly increase a site's risk of injuries in the warehouse.
Accident spike during recoveryAlthough the link between recession and safety is well known as struggling firms come under pressure to cut corners, there is also a less-publicised tendency for accident rates to spike during a recovery.
As my colleague Stuart Taylor of Mentor Performance Risk Management revealed at September's National Fork Lift Safety Conference, the lag between orders increasing and the confidence to invest in additional equipment, people and skills creates a number of additional risk factors.
Notably, those risks include the increased use of temporary staff.
Risks multipliedAgency workers and contractors have their own section in the HSE's definitive forklift operations safety publication, L117 Approved Code of Practice for Rider-Operated Lift Trucks, emphasising that special risk management is required. And with good reason: research shows any worker is four times as likely to be involved in an accident during the first month of their employment, and each percentage point increase in new staff raises a company's risk of major workplace injuries by between 1.7% and 2.5%.
Duty of careL117 is also keen to remind employers of their duty of care to temporary and casual staff: you are no less responsible for the safety of an agency worker on their first day, than you are for someone who has worked for you tirelessly for decades.
In practice, it makes little difference. Accidents rarely happen in isolation, so a new worker who is unfamiliar with a company's safety procedures is as much a risk to permanent staff as they are to themselves.
Verify skills firstParticularly in the case of forklift operators, it is essential to confirm skills and prior experience before they're contracted.
The UK has no such thing as a 'forklift licence', of course, but trained operators will have certificates to show what training they have received. Take the time to check those details with the relevant training provider and accrediting body - and remember that a certificate issued from overseas does not necessarily mean that the holder can operate a truck in the UK.
Whatever the certificates say, the responsibility for their competence still lies with the employer. If there is any doubt, the safest approach is always to arrange a practical skills assessment, and tailor training accordingly.
Training for everyoneDon't limit training to forklift operators, though. About two-thirds of workers injured in forklift-related accidents are colleagues on foot, so safety awareness training for anyone working in the warehouse is a good investment.
Likewise, managers have a legal duty to ensure that they themselves have the skills and knowledge they need to spot risky working practices, and intervene.
Just because a worker is temporary, it's no reason to train them any less thoroughly than full-time staff. Not only will this cut the accident risk, it will also improve their motivation and productivity; often, the skills they need to be safe will also make them more effective and efficient.
Whether they're with the company for one week or a lifetime, investing in skills helps people work safer, and deliver the best possible return. It also makes sound business sense.