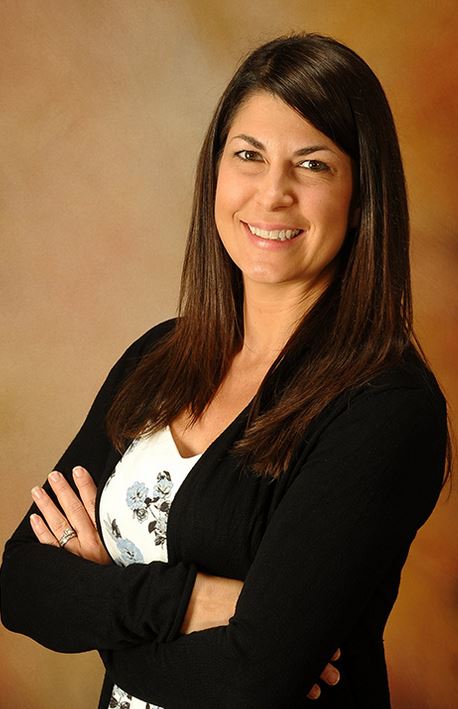 Kristin Lelewicz |
Kristin Lelewicz is marketing manager for Wolter Group LLC, which includes Wisconsin Lift Truck, Illinois Material Handling, Ellis Systems, Wolter Material Handling Corp., Fleet Services and Wolter Power Systems. Kristin brings 15 years of experience in the materials handling industry and is responsible for overseeing marketing and business development efforts across seven brands within the materials handling, power systems, storage and handling, and automation market segments.
Switching to narrow-aisle racking or very narrow-aisle (VNA) racking storage configurations allows companies to store more goods and materials per square foot within their warehouse or distribution centre. This involves narrowing the aisles as well as going higher with your pallet racking to allow for maximum storage capacity.
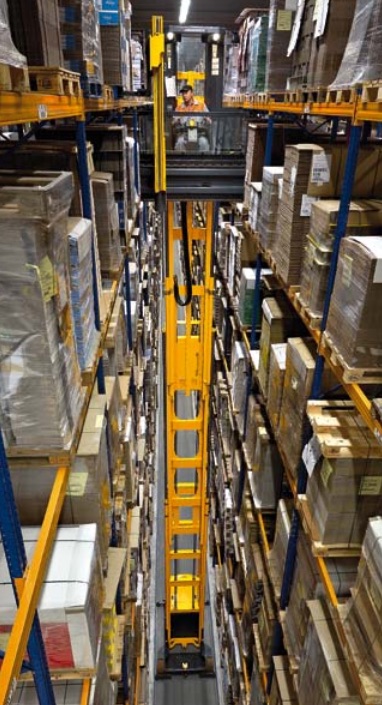 Narrow-aisle solution |
Standard selective pallet racking aisles are at least 12 ft. (3.6 m) or wider. Narrow-aisle racking is spaced from 8 ft. to 10 ft. (2.4 - 3 m) wide, compared to very narrow-aisle racking designs that can have as narrow as 5.5 ft. (1.7 m) aisles, storing up to 50% more product in the same footprint.
Warehouse managers are challenged with improving efficiency and reducing costs and yet still need to find ways to improve or modernise their processes. It's no easy task. Many warehouse managers turn to narrow-aisle racking or very narrow-aisle racking storage solutions to make better use of their existing or new facility's storage space.
Here are eight reasons you should take your warehouse storage to the next level:
1. Significantly improved space utilisation - more pallets in less space
2. Reduced cost per square foot or per pallet stored
3. Eliminates the need for offsite storage
4. Avoids building expansions
5. Improved pick rates
6. Gain direct access to all pallet locations
7. Decreased pallet rack damage
8. Improved forklift productivity