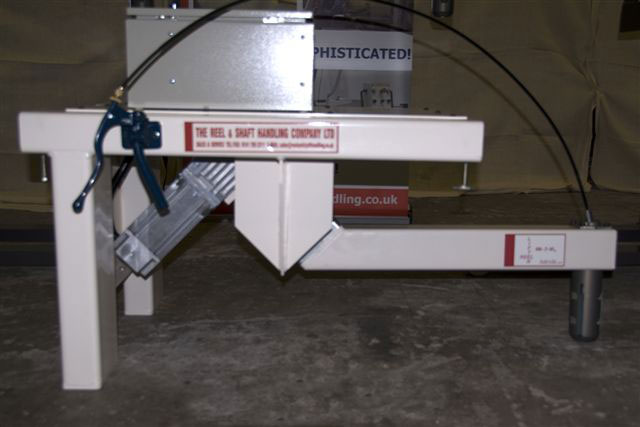 A reel turner that is mounted on fork pockets. |
A UK company has designed reel turners that are mounted on the carriages of pedestrian stacker trucks and on a counterbalanced truck's fork pockets.
The Reel and Shaft Handling Company (RSHC) produced the prototype Reel Lifter Mk3 system after a UK packaging extrusion and printing company commissioned the product. An operator at the company was injured while trying to turn a reel manually. RSHC was asked to design five reel turners capable of handling up to 300kg (661lb) reels by gripping the reels' cores, ensuring that the outer layer was protected.
RSHC already had a range of overhead hoist-mounted reel handling systems. It made the Mk3 prototype by taking the hoist-based Reel Turner Mk2 system and fitting it to a prototype fork pocket support.
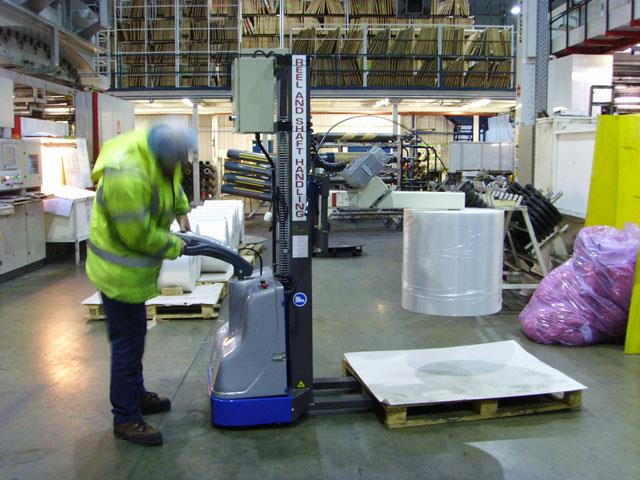 The carriage-mounted reel turner. |
The system was trialed successfully at the customer's factory. RSHC then designed two different versions of the Reel Turner Mk3, four of which were to be mounted on Armanni "Speedylight" pedestrian stacker trucks' fork carriages and a fifth to be mounted onto fork pockets. The latter could be used on any warehouse forklift.
Stephen Weston, RSHC managing director, explains that the design process required several key features to be integrated into both models: "There are two key features that should be built into any good reel turner. The first is that it has to grip the reel securely, absolutely 100% of the times it lifts. In our case. we were designing the Reel Turner Mk3 to pick up in the core of the reel. This meant that we had to use a 'fail-safe' method of gripping the reel with a spring-engaged chuck, which self-engaged as soon as the operator let go of the release mechanism.
"The second key feature that had to be incorporated was powered rotation, as it would be pointless to put in a piece of handling equipment to lift heavy reels and then ask the operator to struggle to manually rotate the reels."
Two versions of the carriage-mounted reel turner were developed. One used a hydraulic rotary actuator to turn the reels and the other version, more expensive and chosen by the customer, used a compact 24V DC electric motor and gearbox to power the rotation.
Weston says both systems required "only minor work" to tap into the stackers' electrical or hydraulic supply. RSHC offers a Reel Turner Mk3 supplied with an Armanni pedestrian stacker that comes with plug-in attachments for both systems.
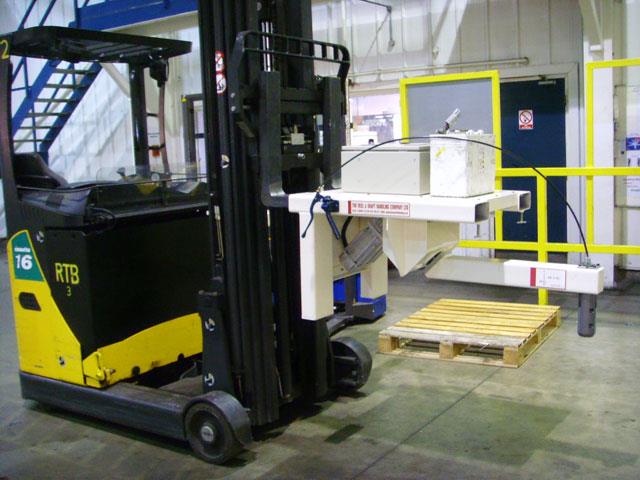 The Reel Turner Mk3 mounted on a forklift. |
However, powering rotation on the fork pocket-mounted reel turner was more difficult. The customer's forklifts had different voltage systems and only several were fitted with extra hydraulics.
The company recognised that future sales could have the same problem, so its designers developed five stand-alone models, each with a different means of powering the rotation: electric-powered from the stacker, electric-powered from its on-board battery, hydraulic-powered from the stacker, hydraulically powered from an on-board hydraulic pump and manually rotated with a hand wheel and gearbox.
Weston says the designs were a result of increasing export enquiries particularly from North America and Australia.
"We decided to make all versions of the Reel Turner Mk3 into compact self-contained units that would be easy to ship and retrofit onto a customer's own stacker anywhere in the world."