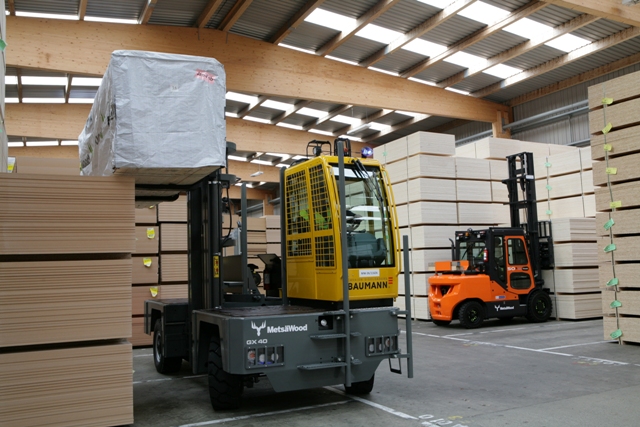 Baumann sideloaders, Doosan counterbalance trucks, JCB Workmax site vehicles and Nilfisk cleaning equipment have been delivered to Metsä Wood. |
Independent dealer Windsor Materials Handling has beaten 10 equipment manufacturers after a six-month tender process to win a long-term nationwide contract to supply and maintain Metsä Wood's fleet of materials handling equipment.
The deal includes the provision and maintenance of 33 Doosan forklifts, 20 Baumann sideloaders, and JCB Workmax site vehicles and Nilfisk cleaning equipment for Metsä Wood's key production sites in Widnes, Grangemouth, Boston and King's Lynn.
During the tender process involving seven potential suppliers and 10 equipment manufacturers, each company was asked to come up with ways of improving an already efficient operation.
Gary Isherwood, Metsä Wood UK's operations purchasing manager, says: "Our commitment to improving our operational capabilities is a key part of our ethos, as is delivering industrial efficiencies across the business. It may make us a more demanding customer, when it comes to materials handling, but we feel it makes us a better supplier to our customers and a better company to work for."
The wood products producer cites Windsor's independent approach and commitment to delivering additional safety, efficiency and fleet management capabilities as crucial elements of their winning proposal.
Efficiencies throughout the supply chain, and changing demands within the construction, industrial and distribution sectors, have resulted in changes to the way Metsä handles its Nordic premium timber, plywood and other core products.
Windsor director Jason Reynold says his company surveyed the way equipment was being used across Metsä's sites and "felt there were several ways in which we could bring efficiencies, whilst adding flexibility and an upgraded operator experience".
As a result, the entire Metsä fleet will now include GPS driver access and monitoring devices, and a host of safety, environmental and ergonomic improvements. Online fleet management from Leicester-based Fork Truck Controls will allow Metsä to monitor equipment usage and accidental damage, stay up to date with costs and access service records.
"The GPS devices provide valuable information for the management team, while additional LED lights, reduced paperwork, upgrades to seats and reduced noise and vibration levels are small improvements that add up to a far greater user experience," Reynolds says.
"Improved fuel economy, reduced emissions and added safety features are all included, and the fleet will be flexible enough to respond to temporary changes or increases in future demand. This is a fleet management solution, not a standard contract for forklifts," he adds.
The companies have also launched a Metsä operator of the year award and challenged manufacturers to redesign parts of their equipment to make it both safer and more suitable to their needs.
"We wanted to look at every possibility. The aim of the redesign of equipment was to increase comfort, safety, environmental impact and fuel efficiency," Reynolds tells
Forkliftaction.com News. "We looked at tyre wear, seat types, truck capacities, engine emissions - anything that might help Metsä achieve greater efficiency.
"The manufacturers were open to making their equipment more suitable to the operation. It was our job to identify the opportunities and challenge them to come up with the right solutions."
Windsor operates from 11 UK branches, offering materials handling and access equipment, for sale, hire and maintenance. Established in 1977, the business claims to be the UK's leading independent supplier of Komatsu, Kalmar and Doosan forklifts, Baumann sideloaders, Atlet warehousing and JLG access equipment.