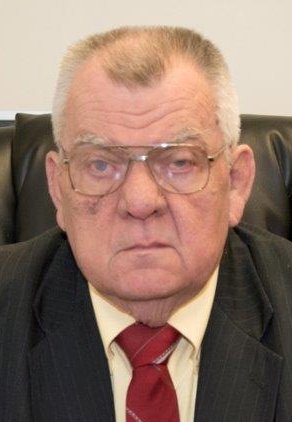 Norman Benjamin |
An advocate for lead-acid batteries does not envision any alternative forklift power source - such as fuel cells - becoming a viable widespread replacement in the near future.
Norman Benjamin, 66, president and co-owner of Bulldog Battery Corp, notes that a large number of battery chemistries have failed in the past for lack of run time, cost or weight for counterbalance.
"Lead-acid is today and, as far forward as I can see, will continue to be the most cost-effective power source for the forklift," he says.
He notes, "The changes we see from the battery manufacturing side indicate that more efficient systems on forklifts better utilise the battery capacity. At the same time, we see the need for increased run time for each truck requiring more capacity."
Opportunity-charging or rapid-charge systems exist. "These systems shorten battery life and require more frequent battery replacement, but the payback, as the customer sees it, is added productivity with fewer pieces of equipment," Benjamin observes.
Benjamin cites examples of past forklift battery technology and how his company's institutional memory can benefit forklift customers. Forklifts account for about 99% of the firm's business.
"The industrial battery has undergone many changes over the years," he says. "Some changes in material specifications have yielded improvements, achieving more consistent raw material allowing for a more consistent product as the end result."
He says some of Bulldog's products were developed before the market was ready to accept them. "The Elite Power battery that Bulldog manufactures, using full-size plates with the same density of active material, is a sample of that," he says. It combines "several products made in the past but given up as not needed at the time"or which could not be controlled.
Benjamin cites material improvements as important to achieve additional run time for forklift users while maintaining the expected battery life. These, he says "will allow approximately 33% additional capacity for the forklift in the same compartment but can deliver the five-year life expected".
A career in the battery businessBenjamin grew up in Kankakee, Illinois where he graduated from high school in 1965 and attended Kankakee Community College. He has taken numerous night courses as continuing education.
In 1969, he began working with Illinois Fabricators Inc, a manufacturer of steel industrial battery cases primarily for GNB Technologies in Kankakee.
"I was the head engineer for the battery tray division, responsible for the design and layout for processing the steel tray," he recalls. "I branched ... into customer service by designing the trays around our tooling and also designing related products to supply the battery industry."
On behalf of his employer, Benjamin did consulting work with the battery companies. "In this association, I became quite involved in the manufacturing of industrial batteries and had a good working relation with many of the engineers and manufacturing QC departments of the battery companies, small and large."
Customer visits with Vic Bakken, an engineer with Chicago Battery in Kansas City, Missouri, whetted Benjamin's interest in the business. "He bent my ear on industrial batteries," Benjamin says. "Vic put the picture together."
John Dawkins was president of Chicago Battery until it was sold to Chloride. "John then moved to Chicago and started Bulldog Battery in 1977," he says. Soon, Benjamin began working for Dawkins, and the two now co-own Bulldog Battery.
In 1985, Bulldog Battery "ran out of building" in Chicago and accepted economic incentives from Indiana to move the business to Wabash in the north central portion of that state.
Now, the corporation employs 97 staff, operates through 300 distributors in the US and several elsewhere and anticipates 5-6% growth in sales for calendar 2013 over last year. "We are seeing a slow, steady increase," Benjamin says.
The vertically integrated operations in Wabash include a tray fabrication facility of 75,000 sqft. (6,968 sqm) and a battery plant of 135,000 sqft. (12,542 sqm).
Depending on a customer's needs, "we will ship on the same day as we receive an order," Benjamin notes. The usual ship time is three days.