Part One - Seegrid Gazette studyAmerican Packaging Automates with Unmanned Seegrid Robotic Industrial Trucks |
The expression "hot off the press" was used more than a hundred years ago, as was rotogravure, a type of intaglio printing process. Rotogravure involves engraving the image onto an image carrier. In gravure printing, the image is engraved onto a cylinder because, like offset printing and flexography, it uses a rotary printing press. Once the backbone of newspaper photo features, the rotogravure process is commonly chosen today by publishers, advertisers, packaging buyers and converters to produce high quality multi-color printing on a variety of materials ranging from film and foil to lightweight coated paper and paperboard.
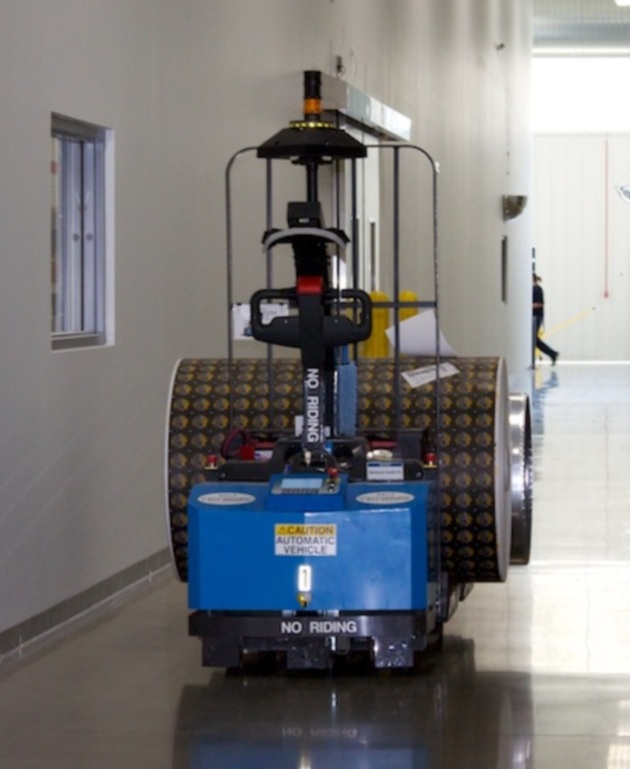 |
American Packaging Corp. (APC) Rotogravure Printing & Laminating Division is growing rapidly. Using 75-foot-long, two-story-high printing presses, ink by the barrel, and computerized systems operated by skilled workers with a keen eye for color, APC creates millions of colorful packages and labels a year. APC prints for famous food products like Klondike Bar, Pringles potato chips, M&M's, refrigerated dough by Pillsbury, and Tyson Chicken.
Located in Columbus, Wisconsin, APC is rated one of the top rotogravure printers of paper and film based flexible packaging specifications in the world. With 240 dedicated employees working in the 400,000 square foot facility, the company turned to Seegrid's unmanned
GP8 robotic pallet trucks. A $17.5 million dollar equipment and facility expansion was completed in 2011, which included a third computer controlled cylinder storage and retrieval system, a new computer controlled slitter, and a custom built Rotogravure Press Laminator with 100% defect detection.
Seegrid robots are essential for APC because the facility features multiple eight and ten color rotogravure presses capable of in-line printing with tandem lamination of film, paper and foil substrates. The robotic pallet trucks transport two printed rolls of work in process from the presses to the slitters weighing 3,000 pounds each.
Seegrid Robots Prove Best Option vs. AGVs or Forklifts |
Automated Guided Vehicles (AGVs) are costly, rigid, and lack the flexibility needed by companies like APC. Part of the growth experienced by APC is the capability to combine several substrates in-line, enabling American Packaging to develop laminations with customized physical, optical, and sealing properties that meet specific product and packaging format requirements.
The wide variety of structures currently manufactured, along with the goal of continuous improvement, led APC to choose robots over AGVs. The flexibility robots provide meets the wide variety and responsiveness required throughout the operation. APC trains a new route with Seegrid robots and it's operational within minutes; that is impossible with AGVs.
The labor costs associated with traditional forklift usage was not an effective option for APC versus the Seegrid robotic industrial truck. The facility layout requires transportation of material over a long distance; there is no need for an operator to navigate this activity. The traditional labor necessary to move material from points A to B is better utilized elsewhere in the plant.
Volume Increases Without Labor Cost Increases APC did not replace any existing equipment because the timing of the installation coincided with the expansion; Seegrid robots were more cost avoidance. With the dramatic volume increases APC has experienced in the past year, the company has not added additional labor or forklifts to handle the volume increase. APC was able to disperse the labor otherwise used to more value-added activities. Purchasing several Seegrid GP8's allows APC to run multiple eight and ten color rotogravure presses, 24 hours a day with no transportation cost internally. The alternative would be a minimum of three or four forklifts and drivers on each shift. |
Part Two - to be continued next week...
Seegrid CorpPittsburgh, PA - USA
Email: sales@seegrid.com
Web: www.seegrid.comTel: +1 412-379-4500