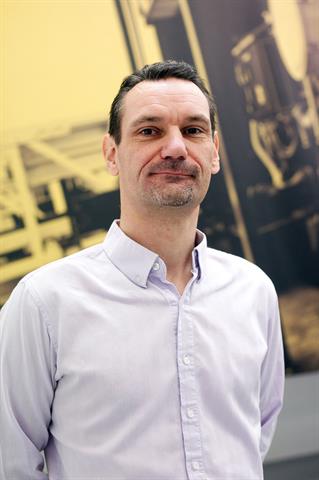 Steve Noakes |
The new EU standard EN1755:2015 is set to impact the design of materials handling equipment intended for use in Zone 21 and 22 hazardous areas, where powders and dusts are present. Food production and storage operations, the chemical industry and many other manufacturing and logistics operations will be affected.
"A spark from unprotected electrical equipment on a forklift, excess heat from the engine, motors, brakes or other components can ignite a layer or cloud of powder in the workplace," says Steve Noakes, engineering manager for explosion protection conversion company Pyroban.
Powders and dusts are found throughout industry as raw materials or as waste, the by-product of a production process. The majority, such as flour, cocoa, milk, polymers and sugar, are combustible, while carbon black, aluminium and other metals are conductive.
A risk assessment will define whether an area where powders or dusts are present needs to be classified as Zone 21 (higher risk) or 22. In classified Zone 21 or 22 areas, specially protected equipment should be used, categorised as either 2D or 3D, respectively. Forklifts are no exception.
"EN1755:2015 will affect the design of forklifts used in Zone 21 and 22 areas in the chemical, food and drink supply chains and in various manufacturing and logistics businesses," Noakes warns, explaining that EN1755:2015 is the standard by which conversion companies like Pyroban convert forklift trucks so that they are safe for operation in hazardous areas and comply with the ATEX 2014/34/EU Directive.
Mandatory from November 2017, the update to EN1755:2015, titled
"Safety of industrial trucks. Operation in potentially explosive atmospheres. Use in flammable gas, vapour, mist and dust", brings together the latest market knowledge and solutions and references the latest standards which were not available when first issued in May 2000.
With regards to static protection, standard seats and arm rests are still acceptable with no additional requirements for plastic parts on either 2D or 3D equipment categories. However, tyres for machines travelling over 6 km/h must be antistatic and there should be conductivity to earth via two straps or conductive tyres.
"Pyroban's solutions for Zone 21 and 22 environments already meet many of the new safety requirements. However we are implementing the full programme in phases during this transition," he adds. "We encourage forklift OEMs and dealers to engage with Pyroban early to ensure they are fully aware of their responsibilities and how these changes will affect them directly."
For electric forklifts, Pyroban's Dust-tec 2D and 3D systems ensure all ignition sources, such as the surface temperature of brakes and motors, remain below the temperature required to ignite either layers or clouds of dust/powder. In addition, arcing and sparking components are enclosed to ensure dusts or powders in the atmosphere cannot be ignited. Non-electrical risks are also addressed by appropriate explosion protection technologies. For diesel powered mobile equipment, Pyroban Dust-mech 2D and 3D provides the necessary safety and compliance, covering both the internal combustion engine and the electrical and mechanical systems within the forklift.
Pyroban systems can usually be fitted to any brand of forklift or similar equipment at the company's factory in the UK or the Netherlands.
"We want to make the transition as easy as possible for forklift suppliers, OEMs and users," he adds. "All levels of the supply chain need to be aware of the changes well in advance."
EN1755:2015 is introduced in parallel to the update to the ATEX Directive and ISO 3691-1:2011 which clearly states that with regards to safety, unauthorised truck modification is not permitted and that no alterations should be made without the prior written approval of the original truck manufacturer.