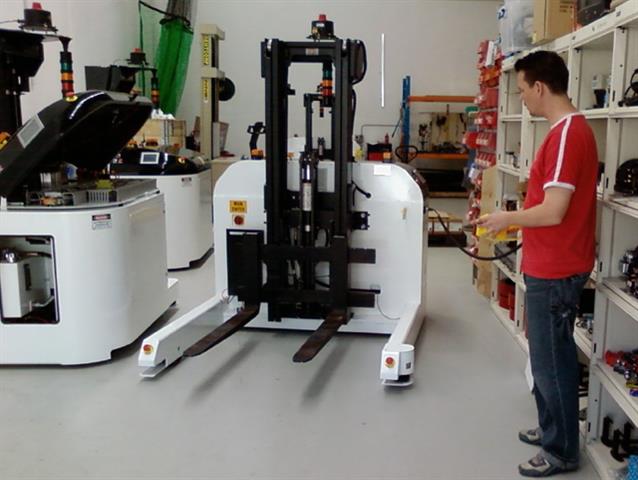 Laser guided vehicle (LGV) undergoes testing |
Laser Guided Vehicles (LGVs) will replace traditional forklifts at the Royal Australian Mint as part of a modernisation program to improve materials handling and safety on the production floor.
The contract, awarded to Australis Engineering of Padstow, New South Wales late last year, involves the incorporation of a wide variety of technologies to work together as a cohesive system. These include laser guided vehicles (LGVs), robotics, automated vision systems, manufacturing execution system (MES) software, conveyors, multi-axis elevators, scanners and labellers.
Director of Australis Engineering, Anthony Gustafson, tells
Forkliftaction.com News that the company has completed around 40-50% of the work involved, with final completion due in March 2009.
The company is responsible for implementing an automated system which will allow the mint to submit a work order that will then automatically set the system to work and allow minimum manual handling in the movement of materials throughout the system.
"The three LGVs, in conjunction with the rest of the system, will replace four traditional forklifts in total and will allow for approximately 1,350 pickup and drop off points for coin blanks, finished coins and associated production materials," says Gustafson.
The LGVs are currently under construction, with initial programming also under way. The machines will have a carrying capacity of 1,500kg and a vertical reach suitable to pallet racks of three high. They will perform a variety of tasks apart from the traditional pallet movements. Movement of palletised product between floors happens automatically, with the LGVs interacting with an eight-tonne goods lift where pallets are loaded and unloaded directly into and out of the lift.
He says the traditional forklifts have in the past posed a serious occupational health and safety risk on the production floor where operators and vehicles work side-by-side. "The introduction of LGVs on the production floor eliminates these risks," says Gustafson.
The use of LGVs also allows for some product movements to occur after hours, in preparation for the next day's production. "This equates to a substantial saving in labour and a substantial decrease in OH&S risk to the Mint, while improving the production capacity of the system," he adds.
Cameras mounted on the LGVs will also provide close up views of the minting process to tourists visiting the facility.