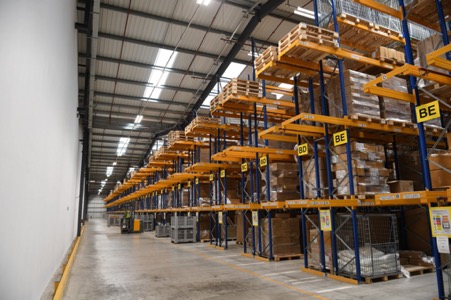 Coach House ordered Jungheinrich's high-rack stacker Very Narrow Aisle (VNA) trucks and five high-level order picking trucks. |
Coach House, the UK's largest wholesale and trade-only furniture and giftware supplier, has automated its warehouse and has upgraded its warehouse vehicles to optimise storage space and maximise its processes.
As a fast-growing company, storage space had been an on-going challenge, and in 2016, Coach House made the decision to expand its warehouse. It was granted planning permission to build a 100,000 sqft. (9,000 sqm) extension, and had planned to recreate the layout of the company's existing warehouse, with a mezzanine floor, and continue to floor stack products.
After a competitive tender to initially fill the extension with pallet racking, Jungheinrich was selected.
Working collaboratively with Jungheinrich to find the right solution for its specific requirements, and following the installation of narrow-aisle racking in the extension of the warehouse, Coach House soon placed orders for two of Jungheinrich's high-rack stacker Very Narrow Aisle (VNA) trucks and five high-level order picking trucks. Two Under Pallet Carriers (UPC) were also ordered to stack larger products too big to go into traditional racking, along with two electric counterbalance trucks.
"With the combination of Jungheinrich's racking solution and trucks, we have been able to truly optimise the additional space the extension provided, as well as maximise the performance and efficiency of our processes," says Coach House director Danny Bovingdon. "We have also been able to increase our production speed and ability to manage increased order volumes."
The company also replaced the old warehouse management system (WMS) with one from Jungheinrich, "due to the built-in functions and flexibility within the system," he adds.
"We instantly found that we were able to introduce better planning and resource management. Another benefit has been that the WMS gives directed instructions to our warehouse operators. The system doesn't quite run itself but, with time spent on setup, rules and configuration, means that managers and supervisors can spend more time on improving our operations rather than allocating basic tasks to staff. Overall, the information from the WMS allows us to achieve better results compared with the old system."
After the upgrade, the company noted an increase in the volume of items being picked (8%), a reduction in the number of hours worked in the warehouse (10%) and has reduced the number of overtime hours needed by 55%.