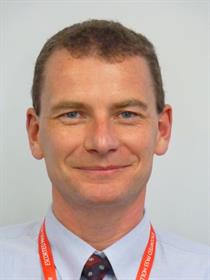 Nick Welch |
Nick Welch is Senior Technical Development Executive for RTITB, the largest forklift training accrediting body in the UK and Ireland, recognised by the HSE, HSA and HSENI.
As many employers will be aware, there is no such thing as a one-size-fits-all training solution. There is also no one-size-fits-all truck solution. When it comes to investments aimed at driving safety improvements and efficiency gains, the nature of your business is a key factor that you cannot afford to overlook. This is particularly the case when you deal with challenging environments such as cold stores, a common setting in the food and drink sector.
The harsh conditions found in cold stores can have a detrimental impact on equipment such as forklifts - harder-working batteries discharge up to 35% quicker than they would in ambient conditions; maintenance costs increase due to faster wear and tear; equipment downtime increases and productivity reduces. RTITB has plenty of tips to help you tackle these issues and keep your operation moving.
1. Equipment selectionNo matter what industry you operate within, choosing the right truck type for the job is crucial to ensure safe operations. When working in a cold store environment, your truck or forklift must be able to cope with and operate within the harsh conditions present. Trucks designed and built specifically for this type of environment have operator safety and comfort at the core of their design, often featuring insulated cabs and heaters. On a mechanical level, bespoke micro switches and motors intended for cold temperatures are used; the oil systems for the hydraulics are filtered to ensure that moisture is trapped before it can infiltrate the hydraulics; and low-viscosity hydraulic oils are used in order to maintain efficiency. All of this adds up to a hardier, safer machine more suited to the environment than a standard lift truck.
2. Safe storage of your machineIn order to prolong use, forklifts should always be parked outside of the cold store when not in use or on charge. When moving from extreme cold to ambient environments, condensation can build on the truck and cause damage and corrosion in components such as lift chains. Conversely, when the truck re-enters cold areas, condensation can turn to ice. Condensation can be minimised by adopting procedures that require lift trucks to pass through a low humidity 0oC temperature area when exiting low or sub-zero areas.
3. Choose the right battery type for your truckBatteries work harder in low temperatures and deplete quickly, so useful operating duration is reduced when compared with ambient operations. To counteract this unavoidable effect, you should opt for the maximum capacity battery available for the size of the truck used. This will help to ensure optimum operation duration, lengthening the interval between charges and reducing downtime.
4. Charge your batteries correctlyBatteries should ideally be charged at room temperature, but always aim for an environment that is warmer than 10oC. This will ensure a more efficient battery charge. To boost battery life and therefore reduce downtime and maintenance costs, batteries should be fully recharged and then, once charged, the battery should remain on charge when not utilised so that it is ready to re-enter the cold area in peak condition.
5. Complete regular maintenanceAny forklift should be regularly maintained to ensure safe use and productivity, but trucks used within cold stores should be monitored more frequently. You should also consider increasing the frequency of LOLER inspections in order to cater for the conditions in which the trucks are operated.
6. Pre-use inspectionsAgain, regardless of industry or operating environment, regular pre-use inspections are critical to safety in the workplace. As well as more common checks, operators should also check for moisture and ice, which could affect electrical components. Care should also be taken if the pre-use inspection is carried out in an ambient setting - surface water that has collected on the ground around the truck due to thawing presents a skid risk when carrying out steering and brake tests. Employers should ensure their operators are trained to complete a thorough pre-use inspection that is relevant to the truck and the operating environment. This should be enforced daily in order to reduce downtime, truck damage and the risks presented by potential mechanical failures during operations.
7. Review your current trainingSpecific job training will not only help you comply with the regulations, but will also help operators tackle the challenging conditions they are likely to face within a cold store environment and the unique characteristics of the equipment they operate. After successful completion of basic operator training and specific job training, drivers should also complete on-the-job familiarisation training within the cold store environment itself. This will allow the operator to put their knowledge into practice, whilst becoming familiar with the area, ensuring that they can complete tasks safely and competently.
8. Keep your operators comfortableOperators shouldn't spend prolonged periods exposed to this type of environment. Regular breaks will improve efficiency and safe operating standards. Ideally, forklifts operated in these types of conditions should be fitted with enclosed, heated cabs, particularly when operators are expected to complete a full shift. But in the event that enclosed cabs or heaters are not an option, operators should be provided with suitable clothing and headwear to keep them warm and comfortable. Warm clothing must not hinder an operator's ability to work the controls, so controls that can be used with gloves, and a cab with good visibility, or even a camera, will ensure operators won't be compromised by restrictive clothing.