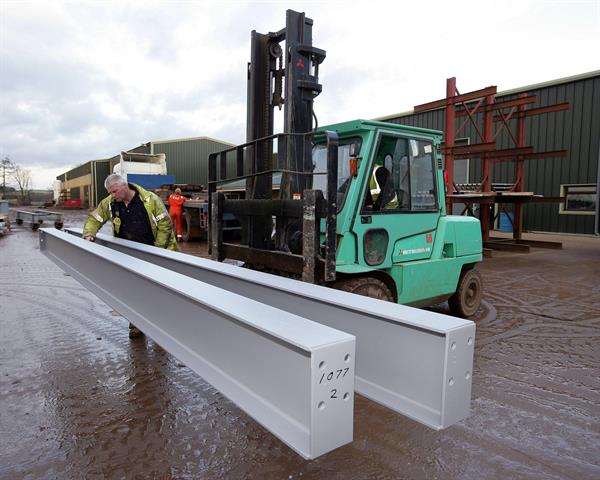 The modified 5-tonne forklift |
A Scottish steel fabrication facility has moved away from sideloaders and telehandlers in favour of modified forklifts to help keep up with production.
BHC Ltd's facility in Lanarkshire was finding sideloaders and telehandlers cumbersome and unable to keep up with the company's growth.
The firm had a goal to expand steel production to 600 tonnes per week but required a more efficient and space-saving solution, so it approached Mitsubishi dealer Douglas Gillespie Plant (DGP) for assistance.
Brian Docherty, DGP's sales manager, says BHC was looking for ways to maximise efficiency and minimise downtime during the 18-hour workdays. "To achieve this, the new fleet had to be reliable, rugged, low maintenance and easy to manoeuvre."
BHC chose a package of four diesel counterbalance forklifts - two Mitsubishi 4-tonne FD40Ks and two 5-tonne FD50Ks.
The forklift cabins were modified to allow drivers to work indoors and outdoors in comfort. A wide carriage and twin wheels were added to one 5-tonne forklift so the weight of long, heavy pieces of steel could be safely spread.
Brian Hewitt, BHC's managing director, has worked with Douglas Gillespie Plant in the past. He says he knew DGP would provide an effective answer to the facility's problem. "DGP were proactive in putting together a package that helped our production levels - and company - grow."