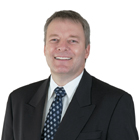 Murray Fane of CHEP Asia-Pacific |
The future for supply chain asset management may lie in Radio Frequency Identification (RFID) which allows individual pallets to be tracked from start to delivery, but most Australian companies are still waiting for the technology to be perfected before embracing it fully.
Perfection is on the doorstep, according to director Murray Fane of CHEP Asia-Pacific, who tells
Forkliftaction.com News that the technology is close to 100% accuracy.
"We have started to achieve 100% reads not just with pallets but also with pallet loads of our plastic crates. This means we will soon have the ability to track goods moving in our crates and other equipment throughout the supply chain at 99.99% accuracy. This is a step change and I expect to see take-up grow exponentially on the back of it."
Fane warns forklift companies to get ready to implement the new technology. "We're so close to 100% accuracy that the market will start to expand quickly.
"Forklifts will play a large part in it and this is because forklift-mounted readers have more time to read the tag as opposed to stationary readers which have to read quickly as a forklift drives past at speed.
He acknowledges the reasons why forklift suppliers have been reluctant thus far to invest in RFID technology. "If their customers cannot see value in RFID, then they are unlikely to pay for it. It also takes substantial technological investment to select the right tag and reader combination and since technology is moving so fast, they will not want to invest in the wrong choice."
However, says Fane, when 100% accuracy can be achieved, preferably using Electronic Product Code (EPC) standards, then it will be far less risky to invest in hardware.
CHEP is at the forefront of the RFID research and took part in the EPC Network Demonstrator Project extension last year aimed at demonstrating the potential of the technology. The project tested the concept of paperless delivery and the use of ePOD (electronic proof of delivery) through EPC.
Fane says that by using ePOD and paperless delivery, process times are cut 49 minutes per delivery, with an additional general administration saving of two hours and 43 minutes per day at a single CHEP service centre.
"We estimate that an end-to-end transaction involves a total turnaround of 175 minutes for both CHEP and the customer. In a controlled environment, ePOD and paperless delivery simplifies the workloads and improves productivity for administrative staff, drivers and other logistics staff."
In the trial, five manual steps were removed from each of the pallet receiving, hire and de-hire processes, including paperwork duplication, data entry and load checking, which benefits both the customer and supplier.
CHEP discovered that in order to achieve 100% read rates, RFID tags have to be designed specifically for the application.
"You need to design the right tag for the item it is tracking and the environment, and you need people who have the knowledge to ensure readers are set to their optimum efficiency. One advantage of using tags on reusable assets is most of this work has already been done by the asset supplier," explains Fane.
The next step for CHEP is to integrate the RFID system with its existing Personal Digital Assistant system (rugged handheld mobile computers), and it is in the process of negotiating with some of its FMCG supply chain customers in order to make the project viable. Says Fane: "Since our equipment moves through the whole supply chain, the real benefit comes when we collaborate with customers on data sharing."
The company is more advanced in the automotive market, and is already installing readers at its automotive service centres, and has tagged its plastic crates that carry automotive parts. "Our CALM system allows us to take production forecasts from car manufacturers enabling us to send our equipment (crates and bespoke equipment packaging trays) to the component supplier at any point around the world in time for them to pack components and send to the production line. This equipment will be RFID-enabled, allowing us to track individual items out from our service centres and back again."