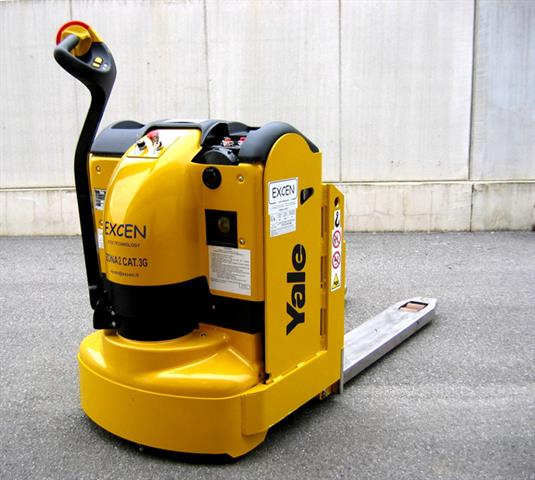 Excen converted Yale |
In March 2008, an explosion at the aerosol container filling plant of Cortec Corporation in Spooner, Wisconsin, USA was thought to have been caused by sparks from an electric forklift igniting gas in a zone 1 environment. The production room was destroyed and several employees were badly injured, one with second- and third-degree burns to 80% of his body.
A recent report by Marty Ahrens of the National Fire Protection Association (NFPA), a USA regulatory body, listed 1,340 structural and vehicle fires per year for between 2003 and 2006, in which industrial loaders or forklifts were directly involved in ignition.
Zones, divisions, classes and groupsHorrific accidents like that at Cortec and an increasing number of workplace explosions and fires have alerted the materials handling industry and its users to the need for much stricter regulations regarding workplace safety and the explosion-proofing of equipment used in high-risk areas.
High-risk areas have been defined as those areas with a potential risk of explosion from gas vapours or from dust. Areas are divided into internationally recognised zones; there are three zones for gas and vapours and three zones for dust:
Gas and Vapour Zones
Zone 0This is potentially the most dangerous working area, the presence of an explosive gas atmosphere is constant, frequent or for a long period of time.
Zone 1An area in which an explosive gas atmosphere might be formed during normal functioning.
Zone2An area in which an explosive gas atmosphere might occur for a short time or not at all.
Dust Zones:
Zone 20An area in which an explosive atmosphere formed by dust is present constantly, frequently or for a long period of time. Layers of dust do not form a zone 20 if they are not present constantly, frequently or for long periods of time.
Zone 21An area where a potentially explosive dust cloud is formed during normal working hours. This zone might include areas near to the dust loading and unloading points, areas where dust might be deposited and areas where there is high possibility of explosive concentrations being formed.
Zone 22An area where there is minimal risk of an explosive dust cloud forming during normal working hours. If it should occur, it is for a short period of time. This zone includes areas near equipment, protective systems and components containing dusts from which dust may escape and deposit itself.
In Europe, zones are further divided into gas groups according to their properties and in the US they are divided into classes, divisions and groups. The rest of the world follows one or other of the classification systems.
Regulation confusionDefining zones is as far as international co-operation in regulation seems to go. In Europe, standards are legislated by Atmosphères Explosives, ATEX, and certified by the International Electrochemical Commission (IEC). In the US, there are a number of regulating bodies including the National Fire Protection Agency (NFPA), the Occupational Health and Safety Administration (OSHA) and a number of certifying bodies, including The National Electrical Code (NEC), Factory Mutual Research Corporation (FM) and Underwriter's Labroratory (UL). In Australia, the three recognised certification bodies are Simtars, Testsafe and International Testing and Certification Services (ITACS).
In the US, Australia and other non-EC countries, certification is largely self-regulatory, much to the frustration of people like Robert Zuiderveld, general manager of Pyroban, and James Walker, director of Australian Flameproof Services (AFS) who both believe that clear international standards and safety regulations, and a central certifying body in each country, are imperative to workplace safety.
They both lament the confusion surrounding regulation and certification. As Zuiderveld wrote in a recent article for Fireworld, "due to code interpretation and explosion, hazardous areas rating variances, adequate levels of regulation and worker protection have not been established".
Walker adds, "Without proper testing by a suitably recognised authority (third party), how can you be sure that the equipment you are manufacturing is not a danger? Self-testing is not certification and should not be mistaken as such."
What is an EX forklift? Landoll-Drexel Ex modified forklift |
An explosion- or flame-proof forklift (EX) is one which has been modified or built from the ground up for use in zones 0, 1, 20 and 21. These include mining tunnels, oil and gas platforms and production plants; chemical, paint and perfume manufacturers; grain, sugar and cement silos and production facilities; and ammunition stores. As Malcolm Davis, business development manager for Pyroban, explains,"in explosion-proofing, the basic principle is to eliminate the forklift as a source of ignition in these zones".
Sources of ignition are almost as many as the parts on a machine, including electrical and non-electrical components, electrostatic charges, hot surfaces and exhaust systems.
Both diesel and electric forklifts can be built or modified for EX use. Petrol and LPG equipment are prohibited from hazardous areas due to the inherent risk of ignition. According to Patrick Richardson of Rico, electric EX forklifts dominate the market with diesel making up only 1% of the North American EX fleet. Explosion-proof forklift manufacturer Landoll doesn't even make a diesel machine, believing that electric forklifts are more versatile.
Standard protection techniques applied to equipment can be recognised by the EX initials, followed by a unique set of initials which describe what modification has been made and in what zone the machine is modified to work in:
Exd - Flameproof
Exe - Increased safety
Exi - Intrinsic safety
Exm - Encapsulated
Exn - Non-sparking
Exs - Special protection
Explosion protection modificationsTo ensure equipment is explosion-proof, five basic methods are employed: exclusion, containment, dilution, energy limitation and reducing the possible causes of ignition.
Protection issues should be addressed at both the machine and environmental level. For this reason, close co-operation between equipment manufacturer/modifier and end-user is essential. Laurie Davis of Chess Engineering suggests that when ordering a flame-proof forklift, the customer should always specify the area classification, the type of hazard and its temperature class.
Exclusion means that the explosive atmosphere is prevented from entering equipment and contacting the source of ignition. This is achieved by explosion-proof coverings which are either screwed or bolted on and made from steel or resin. Although gas sensors do not exclude gas from entering the machine, they quickly alert operators of a potentially explosive environment. Technology such as Pyroban's Gascheka tests ambient gas levels and automatically shuts down or de-energises the equipment if 25% LEL (lower explosive limit) is detected. The Gascheka can be retro-fitted to both diesel and electric forklifts.
Excen produces an integrated gas sensor system that eliminates the need to carry the calibration gas bottle on board, thereby making it a safer option in zone 1 areas.
Containment refers to any explosion being contained within the equipment so as not to make contact with the surrounding atmosphere. Again this can be achieved by flame-proof coverings around sites of possible ignition, such as batteries, engines, wiring, exhaust systems and cables. Rico uses a mineral insulated typeM cable on all its machines, which is flame-retardant. All enclosures must have a length fitted so that any flames occurring within the enclosure are snuffed out and hot gases cooled before reaching the outside.
Dilution, ensuring the area containing the equipment is well ventilated, is the responsibility of the end-user, although fitting of gas detection sensors certainly aids in ensuring a safer environment.
Energy limitation, reducing the energy within equipment and its circuitry so that cooler temperatures are maintained, is achieved by equipment such as Miretti's integrated thermostat which automatically shuts the forklift down if the engine reaches 85˚C. Other technical options include integrated cutout switches for batteries and thermostat sensors in other parts of the machine such as exhausts and manifolds.
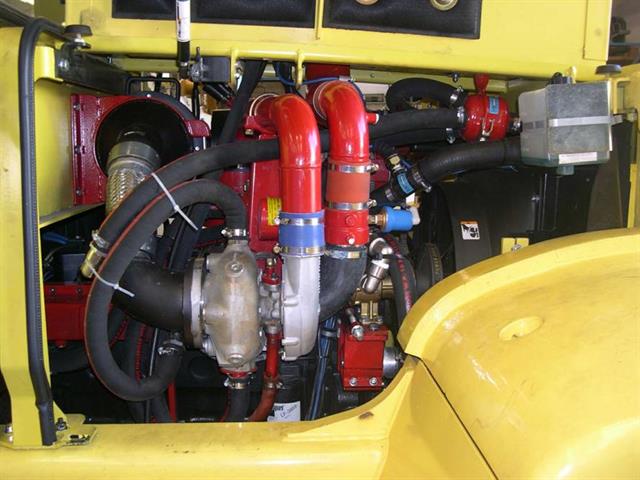 Hydronika Ex modification for turbo engine |
Robin Chapman, principal engineer at Pyroban, has seen an increase in turbo-charged diesel forklifts being used in zones 1 and 2. This is of some concern, he says, as they are typically uncooled and generate extremely high operating temperatures. Chapman says that Pyroban has developed a unique water-cooled turbo-charger with explosion protection which overcomes these problems while still maintaining engine power.
Reducing the risk of sparks and static electricity is probably the easiest part of explosion-proofing a forklift. Accessories from the bottom up are available from static-conductive tyres, some with built in heat and wear sensors such as those developed by Miretti, to forks sheathed in brass or stainless steel. All metal and plastic surfaces can be painted with anti-static paint and seating covered in anti-static fabric. Excen diesel trucks are fitted with flame-proof inlet and exhaust manifolds and Airmeex fits its machines with self-cleaning manifolds, which reduce the risk of flammable build-up.
Explosion-proof forklifts are expensive to buy or modify and maintain and, as a result, make up a very small percentage of overall forklift sales. Like the rest of the forklift market, they have been hard hit by the global financial recession, with some estimating a drop in sales of up to 40%. Despite this, the market has seen recent and cautious sales growth. Many in the industry believe this is due to tougher regulations in regard to hazardous work environments and increasing industry awareness of workplace health and safety issues.
As Zuiderveld puts it,"even though the technology is available for those who need it, it is the safety culture and corporate mindset that needs adjustment. With the right mindset, investment, minor equipment modifications and fine tuning of site processes and permit schemes, significant progress in safety can be made. This will not only reduce the risks of fire and explosions, but also protect people, their investment and our environment."