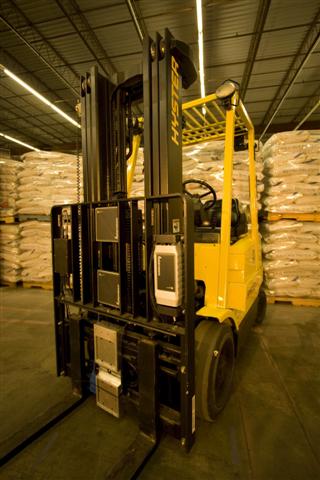 RFID technology has been deployed with Yale and Hyster forklifts |
Rush Tracking Systems has sold 50 of its VisiblEdge radio-frequency-identification (RFID) forklift truck packages for deployment in five unique and different situations. Rush has invested more than USD350,000 in developing VisiblEdge.
"We have deployed on Yale and Hyster trucks" and can deploy on any forklift, says Chuck Thompson, vice president of sales and marketing.
The initial deployment occurred in mid-2007. Now, systems operate, or are in development for, three US-based customers in defence logistics, heavy industrial equipment manufacturing and paper mill processing.
"People have been excited about the value proposition of RFID for a long time," he notes. "The open technologies available on EPCglobal standards have created products that allow for multi-vendor systems to be put together." EPCglobal, a joint venture between GS1 of Brussels, Belgium and GS1 US of Lawrenceville, New Jersey was set up to achieve worldwide adoption and standardisation of electronic product code technology.
Difficulties in achieving operational compatibility existed prior to implementation of the standards.
Lenexa-based Rush was formed in 2003 and obtained strategic funding in 2007 to develop the VisiblEdge turnkey hardware, software and integration solution including input from three individuals who worked on an early version of RFID. Rush has and have human resources with multiple years of RFID forklift experience.
"Knowing an asset is within the four walls of a facility may give you half of the value, but VisiblEdge can deliver 50% more, knowing the location of the asset and validating move instructions," Thompson says.
RFID readers at portals may cost less than VisiblEdge but, typically, may not deliver the same value. "It is more effective to deploy four VisiblEdge solutions than 25 portal systems," he notes.
Now, a truck-mounted load backrest with RFID hardware can be moved between forklifts.
With Rush input, Cascade Corp of Fairview, Oregon created standard part numbers for bolt-on and screw-down load backrest hardware suitable across the forklift industry. Cascade manufactures forklift attachments, forks and accessories.
Regular VisiblEdge-specified forklift components on the load backrest include two cargo antennas, an industrial grade RFID reader, a rugged rack tag antenna, a floor tag antenna and a cargo presence lift sensor. The vehicle-mounted terminal is located separately for operator viewing. A trained user can install a load backrest on a forklift in about four hours and, as needed, remove the fully equipped backrest in about two hours for use perhaps on another rented or owned forklift. A move involves disconnecting and reconnecting wires to the power source, terminal, reader and antennas.
With a prospective customer, Rush conducts an RFID feasibility assessment evaluating business processes, the cost of technologies to support changes and the financial return on investment (ROI). Knowing the ROI helps prioritise activity and focuses on business value to "get the most bang for the buck," he says.
For the Fortune 100 heavy equipment maker, for example, Rush leveraged EPCglobal tags to deliver a 27% return on investment in replacing a manual, labor-intensive, error-prone tracking process. The solution provides the manufacturer with 100% visibility to RFID-enabled Kanban replenishment bins in loops between the original equipment manufacturer, a logistics provider and a contract paint supplier. Kanban is a Japanese-originated concept relating to lean and just-in-time production.
Rush views itself as vendor neutral and aims to select the most appropriate integration solution for a specific client. "We leverage off-the-shelf tags, readers, antennas and industrial terminals and add VisiblEdge software," Thompson says.
Typically, Rush specifies RFID hardware from privately held Alien Technology Corp of Morgan Hill, California or publicly traded Intermec Inc of Everett, Washington.