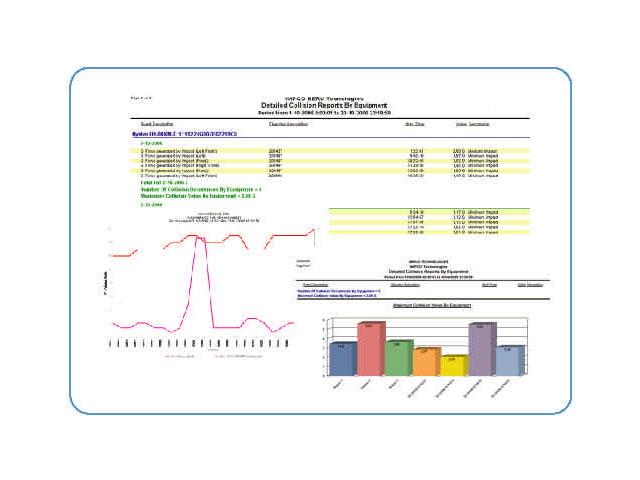 A sample collision report generated from data collected by Impco's FM impact sensor |
Fleet management systems can make workplaces safer and cut costs through efficient management of forklifts. The technology, adopted from other equipment sectors, allows fleet owners to concentrate on their core business, secure in the knowledge that their capital investment is being put to good use.
Christine Liew reports.
IntroductionIn simple terms, a fleet management system consists of on-vehicle hardware and user software that monitors equipment and operators to cut operational costs and improve workplace safety.
Impco-Beru Technologies BV sales manager Roel Vermeulen said it started with car and truck fleets. Car and truck rental and leasing companies needed to provide customers a tool to manage maintenance costs.
He said operational cost, which is the cost of forklift fleet maintenance and repairs, and workplace safety, were direct drivers for fleet management systems.
"Forklifts typically drive around in harsh industrial environments and damage occurs to trucks, goods and warehouse," he said.
Greg Smith, vice president of ID Systems Inc, said fleet management systems were typically used for all types of forklifts, many types of powered industrial vehicles, aircraft ground support equipment and motive power systems.
Smith estimated there were about three million powered industrial trucks operating in North America and a similar amount in Europe. Half of the trucks were in fleets that would be suitable candidates for fleet management systems.
Why fleet management?ID Systems Inc was established in 1993 by engineers from Stanford University. Last year, it was ranked 107th in the Deloitte "Technology Fast 500" list for the second year in a row. ID Systems had a five-year revenue growth if 1,959 per cent, increasing revenue to USD24.7 million in 2006 from USD19 million in 2005.
Last year, ID Systems finalised a strategic agreement with NACCO Materials Handling Group Inc to market and distribute its system via NACCO's dealer network for the Hyster and Yale brands. ID Systems also worked with Linde Material Handling to facilitate a fleet management system sale to international forest products company Weyerhaeuser. The Hackensack, New Jersey-based ID Systems also established its European headquarters in Germany that year.
According to company vice president Greg Smith, there are three main reasons motivating industrial equipment end-users to manage their equipment efficiently.
US Occupational Safety and Health Administration statistics attribute 100 deaths and 100,000 injuries annually in the US directly to powered industrial truck incidents. Fleet management systems can improve the safety and security of employees. By monitoring forklift use, forklift operators instinctively increase awareness of safe equipment operation. It also ensures only trained operators are allowed to operate the vehicles. A safer workplace means lower compensation costs and lowered risk of exposure to liability.
Secondly, the greatest expenses for an equipment user are the capital costs to acquire it and the labour costs to operate it. An average forklift costs between USD20,000 to USD30,000, with specialised forklifts like very narrow aisle trucks costing more. In a two-shift operation, between USD50,000 to USD200,000 is spent annually on the forklift operators' wages and social security benefits. By analysing data of forklift use and measuring productivity, an organisation may decide to reduce its forklift fleet size, hence decreasing both its capital and operating costs.
Thirdly, annual maintenance costs can reach 10 per cent to 20 per cent of the equipment's acquisition cost. A fleet management system provides timely information on the health of the equipment, allowing for efficient maintenance planning. By controlling equipment down time, a fleet management user can keep equipment running and maintain productivity.
Fleet management toolsImpco-Beru Technologies BV, a subsidiary of Impco Technologies Inc, is headquartered in Delfgauw, the Netherlands. The developer of fleet management systems and components has offices in England, France and Germany and sells its systems to end-users, importers and dealers.
Impco-Beru's fleet management system was specifically designed for industrial and materials handling applications and sales manager Roel Vermeulen said a major benefit of Impco-Beru's fleet management approach was its ability to equip mixed fleets with a single system.
He said OEM fleet manager systems mostly work only on the original equipment and do not communicate with competing systems. In contrast, with Impco-Beru's systems, "installation is independent of vehicle make or type or engine".
"We believe fleet owners do not want to restrict themselves to just one make and still want full control of their vehicle fleets and operators with one system," he said.
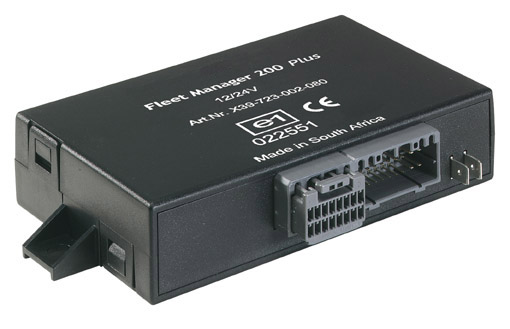 The Impco FM200+ on-board computer |
Impco-Beru's fleet management system consists of an on-board computer that records forklift and driver performance data and user-defined events; a waterproof kit that protects the computer against harsh conditions like steam cleaners; and an impact sensor that measures collisions. The data is then communicated wirelessly by GSM, GPRS, DECT or WiFi.
Through reports that appear on a desktop computer, the person responsible can know exactly when the forklift was running, idling and when certain events occurred. The fleet management user can define which events will be in the report - for example: speeding, collisions and battery disconnections. Reports generated from data collected by the impact sensor can identify the best drivers or any equipment affected in collisions.
Detailed analysis of impacts will also show what speed was driven at time of impact, which part of the vehicle was affected and who was driving. The system can also automatically generate warnings when pre-set collision values are exceeded. Event warnings like severe shock or high engine temperature can also be reported via SMS or email to supervisors.
Meeting customer's needsAustralian-owned Baseplan Software Pty Ltd provides a fleet management system that centres on the operational processes of a business - mostly to fleet management service providers like National Fleet Network, Linde and Toyota Material Handling.
Baseplan business development manager Jason LeGuier said "customers are now becoming better educated about the advantages of a fleet management system".
LeGuier said like many other business processes, the main challenge in selling fleet management systems is helping customers recognise that discipline was essential in gaining the advantages of fleet management.
"Fleet management is about better business processes and not cutting corners. If a company wants to continue to cut corners, then they haven't fully understood the benefits of what fleet management will do for them and the advantages in terms of profit, up time and reduced stress."
Le Guier, however, warned against suppliers promising that their system will reduce operating costs. "It's not the software alone that makes the difference. Many companies we speak to have doubts as to exactly what advantages they will see and how."
Vermeulen from Impco-Beru said fleet management system providers found it challenging convincing customers that fleet management systems had short pay-back times.
"The initial investment of a fleet management system is about EUR1,000 (USD1,348.19) and a new forklift typically costs between EUR20,000 to EUR25,000 (USD26,936.90 to USD33,704.90). This works much better for trucks where the equipment is much more expensive.
"We have seen a return of investment of 1.5 years in our customer base but this, of course, depends on the customer's dedication to using the management information in an effective manner," he said.
While the financial benefits may be difficult to quantify, Vermeulen said improved safety in the workplace was immediate for Impco-Beru customers. Improved safety awareness in forklift users who know they're being monitored has resulted in "dramatic decrease of collisions and accidents" without affecting efficiency.
ID Systems' Greg Smith said many customers "don't know or think they have any problems to solve", so illustrating the experiences of other system users worked well to overcome their objections.
"The real challenge is balancing the potential features and options with the business problems the customer needs to solve. This is consistent with [fleet management] for all types of equipment," he said.