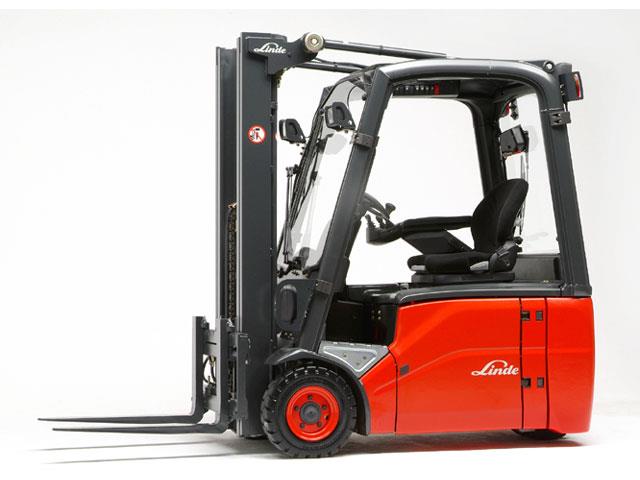 The Linde E12-E20 forklift |
Climate change is a hot topic. The Intergovernmental Panel on Climate Change, established by the World Meteorological Organisation and the United Nations Environment Program in 1988, met in Bangkok, Thailand, this week to discuss and accept one of its working groups' reports, titled Mitigation of Climate Change. According to an industry source, the report's findings say humanity has until 2020 to prevent the earth's climate from collapsing. That is why any contribution from forklift manufacturers to reduce greenhouse gases counts.
Forkliftaction.com News spoke to Toyota, Linde, Jungheinrich, Still and Kalmar about their efforts.
Manfred Höhn, Linde Material Handling GmbH & Co KG marketing service manager, said the German company had kicked off a new marketing label for its forklifts at the Bauma trade show in Munich last week.
"Our answer to current environmental and health issues is Linde PureMotion."
He said Linde PureMotion was an umbrella term covering Linde's design principles and other solutions that reduced energy consumption, lowered emissions and enhanced eco-friendliness.
Linde introduced the E12-E20 electric forklift range in 2006, claiming it was setting benchmarks for energy efficiency.
The electric forklift range, based on Linde's electric counterbalanced 39X series and R14X to R17X reach trucks, was the first forklift for the European market to have an on-board battery charger. Linde's engineers spent 3-1/2 years developing technical innovations in the drive and control units to produce energy savings.
Höhn said Linde created an E-Indicator, the value of which was the load throughput time multiplied by the forklift's energy consumption.
"This is the first efficiency index for the materials handling industry. In a lorry working cycle, Linde's E-Indicator value [for the E12-E20 range] is ahead of the competition."
All Linde diesel forklifts, from the H14 forklift with 1.4 ton capacity to the 52-ton reach stacker, have "modern direct injection" that lowers carbon dioxide emissions. Höhn said gasoline was "injected right into the combustion chamber of each cylinder leading to the most efficient use of fuel".
Linde is conscious of saving energy in its facilities. About 90 per cent of energy consumed by air compressors in Aschaffenburg's Plants I and II is wasted in the form of heat. The heat is recovered and used to produce hot water for staff showers or the cafeteria kitchens.
A monitoring system at Linde's facilities ensures excess demands on the electric power supply, caused by energy consumption peaks, are eliminated by the forced shutdown of the equipment responsible.
"Savings attainable in the heating energy requirements of our Plant II alone come to 16 million kilowatt-hours, equivalent to recovering 60 per cent of total energy input for multiple use or the annual heating needs of 140 single-family houses," Höhn said.
Toyota Material Handling USA (TMHU) is also committed to a cleaner environment. This year, it announced it would make a donation to the Arbor Day Foundation to have a tree planted in a national forest for every 8-Series forklift delivered. Toyota says that is just one of its environmental initiatives.
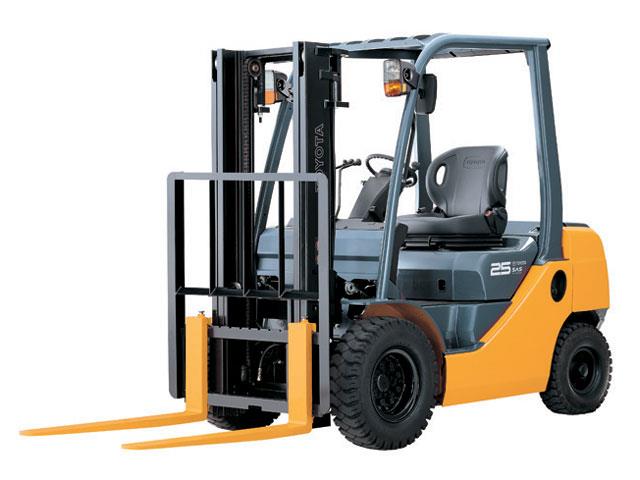 Toyota 8-Series forklift |
TMHU is proud of the 8-Series forklift line, which includes 3,000lb-6,500lb (1,360.8kg-2,948.4kg)IC cushion and pneumatic tyre models. The forklift "far exceeds" 2007 US federal Environmental Protection Agency (EPA) emission standards and TMHU CEO Shankar Basu said the forklift met California's 2010 emission standards three years early.
Toyota's 4Y engine features a closed-loop fuel system that automatically adjusts and optimises the air-fuel mixture ratio. The system works with a three-way catalytic muffler to minimise emissions like hydrocarbons, nitrogen oxides and carbon monoxide.
TMHU claims all Toyota 8-Series gas, LPG and CNG forklifts produce 70 per cent fewer smog-forming emissions than the 2007 federal EPA standards.
Toyota's fuel cell FCHV-F forklift prototype, showcased at CeMAT, in Hannover in October 2005, uses hydrogen as its main power source, produces electricity without combustion and generates zero carbon dioxide emissions. Toyota said in a statement that it was continuing to advance its fuel cell technology and envisaged bringing a fuel cell forklift to market "in the next few years". The prototype was developed by Toyota Industries Corp in cooperation with Toyota Motor Corp.
From April 16 to April 20, Europe's leading multidisciplinary research centre, Research Centre Jülich, presented a new fuel cell concept at industrial technology expo Hannover Messe, in Hannover, Germany. The direct methanol fuel cell technology was currently being tested on a Jungheinrich forklift.
The research group comprises Jülich, Jungheinrich AG, Ritter Electronik (control and performance electronics), AKG Unternehmensgruppe (heat exchanger) and EBM-Papst (ventilators). Management Engineer GmbH & Co KG is the consultant for the research group.
Henrik Schröder, a Jungheinrich-provided spokesperson on the new technology, said the main difference between hydrogen and methanol was that hydrogen was normally gaseous while methanol was in a liquid state.
"The infrastructure for handling liquid fuels, like gasoline or diesel, is standard all over the world and therefore very cheap.
"Methanol only requires minor changes to today's refuelling technology, whereas refuelling gaseous hydrogen requires special equipment for high pressure of more than 300 bars, leading to high investment and operational costs for compressors, for example," Schröder said.
Methanol had a "significantly higher" energy density than hydrogen. That meant longer intervals between refuelling could be achieved. Technical restraints and costs, however, limited direct methanol fuel cell technology to applications in the "low power range". The technology could, in future, be used in electric pedestrian trucks and electric pedestrian stackers.
Schröder said hydrogen fuel cell technology would be market-ready earlier than direct methanol fuel cells that were still being researched. However, hydrogen fuel cell and methanol fuel cell technologies could be used together to power large fleets of different types of forklifts.
"Hydrogen can be easily derived from methanol through a simple chemical process called steam reforming.
"A fleet operator can, in future, use methanol as the primary energy carrier for small trucks and derive hydrogen from methanol at the site to power large forklifts," he said.
Hamburg, Germany-based Still Company made environmental and driver protection the centrepiece of its Bauma presentation.
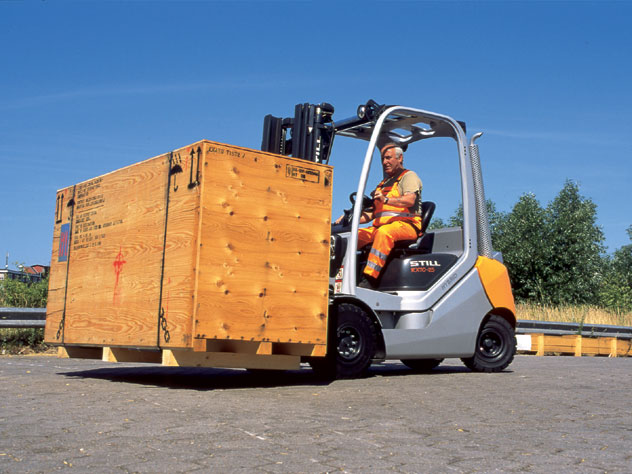 Still's hybrid RX70 forklift |
Still says its RX70 diesel truck, introduced in October 2006, is the first in the world to be equipped with a hybrid drive. It consumes 2.5 litres per hour and emits 6.4kg of carbon dioxide for each hour of operation. (According to a transport emission model developed by a German research institute in 1999, an average passengar car travelling at 50km/h emits 9.9kg of carbon dioxide per hour.) Still claims the RX70 is the most economical forklift of its class; the less fuel it consumes, the less carbon dioxide it emits.
Still senior vice president Bert Frisch said:
"Our products and company traditionally have a very high green factor. We are happy to have the world's best diesel truck in carbon dioxide emissions."
The RX70's hybrid drive unit has a diesel gas engine that drives the generator to produce electricity that in turn feeds the electric traction motor. A hydraulic variable displacement pump that feeds hydraulic oil into the hoist and steering system, only when needed, contributes to fuel savings.
Cargo handling equipment specialist Kalmar Industries, of Stockholm, Sweden, is doing its part to protect the environment. Kalmar undertook a USD1.2 million, two-year project in 2006 with the West Coast Collaborative of the US EPA and the ports of Los Angeles and Long Beach to reduce pollution in ports. By integrating three Kalmar terminal tractors with hybrid technology, air emissions are expected to be reduced significantly. The project is part of the San Pedro Bay Ports Clean Air Action Plan that aims to reduce emissions and associated health hazards resulting from port operations in the next five years.
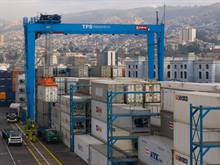 Kalmar's all-electric RTG |
Kalmar spokesperson Elizabeth Gibson said Kalmar was in the research and development phase of integrating the terminal tractors with hybrid engines. There were currently more than 24,000 terminal tractors operating in North America. Kalmar had more than half the terminal tractor market share.
The all-electric RTG, the E-One that Kalmar introduced in 2005, was the first RTG that did not need hydraulics. The design offered fuel savings of up to 30 per cent, based on intelligence in RTG movements; crane speeds were adjusted according to the load under the spreader. Conventional RTGs' hydraulics run constantly but, in the E-One, electrical power was used only when needed, Gibson said.