WEIGHING systems for forklifts are becoming more up-front in today's materials handling industry, and importantly, they are playing a leading role in the overall efficiency of the modern warehouse. A good system can save hours in a busy setting, and maximise productivity and efficiency for logistics companies, reports DAMIEN TOMLINSON in this first of our two-part series.Most of the world's greatest inventions have been borne out of necessity, evolved through the ingenuity of one mind, tested, honed and copied by many, and given a verdict by the toughest of critics, the public.
Forklift weighing systems have been around for more than 30 years in some form or another and the public's verdict (in this case the systems' users) have demanded ever-increasing accuracy and reliability. However, while the products have changed with new technology over the years, the basic purpose has remained the same: to provide an accurate representation of the weight of the load being lifted.
The first of these systems is impossible to miss: a large, 6-inch diameter, analogue dial bolted to the forklift frame, with a pressure sensing device attached to the forklift's hydraulics. Many of these systems still exist, and when they were first introduced, they provided an instant, if only indicative, measure of the load. But they provided the platform for a whole new section of the materials handling industry to be born - "legal for trade" (LFT) accuracy for a broad range of lifting systems.
The search for LFT accuracy has emerged because the biggest factor affecting weighing systems, and something that is driving the research and development in this area, is that the variables from truck to truck and from site to site, make it impossible to produce an "off-the-shelf", one-size- fits-all, system. Hydraulic pressures, load centres, mast height and condition all contribute to reducing the accuracy of weighing systems, hence the technological challenge for makers of these systems is achieving LFT accuracy.
Jacob Blom, export manager with RAVAS BV of Zaltbommel in the Netherlands, said the biggest breakthrough in recent times was providing greater LFT accuracy.
"That means the units are stamped, meaning the end user can use the weight displayed by the system as a basis for an invoice for customers," he said. "This gives companies the capability to lift, transport, and weigh the goods in one action and put all data through a radio frequency system, directly into the computer network, making it all a 'real-time' activity."
Blom said there are three products used for mobile weighing: hydraulic monitoring, which was low-cost and low-accuracy, and used mainly to monitor overloading; attachment plates, which were pricey but 'reasonably accurate', and were effective systems for forklift attachments like clamps and rotators; and weighing forks, which were reasonably priced and offered high accuracy.
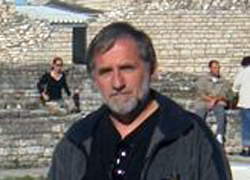 Ted Jurca ... safety simplicity, reliability |
Ted Jurca, president of load cell maker, Integrated Visual Data Technology Inc of Toronto, Canada, said the major priorities affecting the purchase of a mobile weighing system for warehouse customers are safety, reliability and simplicity.
Jurca's business, which sells the Skidweigh line of products, is currently focusing on providing weighing systems as a safety initiative in the USA, where safety of operators, stock and machinery is all-important to the big customers.
"Forklift drivers themselves are responsible if the forklift tips over or there is an accident due to overloading, so companies are making moves to prevent this by using warning systems," he said.
"The systems are quick and easy to install and maintain, and are very simple to operate - customers need simplicity and reliability, and it makes sense. Would you drive your car if it didn't have a speedometer?"
Companies were using Skidweigh products as an overloading warning and weight verification tool. So, if a pallet has a 2800-pound weight sticker on it, the forklift can provide a 99% accurate verification. For overloading, the system is geared to trigger a warning strobe if the load weight is above a pre-defined parameter.
"Overloading monitors can also save millions of potential dollars if warehouse racking is overloaded," Jurca said. "Companies need to know how much weight their trucks are shifting around."
A big problem in finding the right weighing system is that they are difficult to fit at the time of the forklift's manufacture, as customers regularly fit after-market masts, carriages and other attachments post-purchase.
The Skidweigh ED2 is a solution to this problem, and can be fitted to any new attachment after a simple recalibration process. According to Jurca, "it's the only on-board weighing system found in multiple instances in the same company".
"It's almost impossible to devise a system that is legal for trade, and that will guarantee accuracy over a period of time," he said. "The environments that forklift users subject their machinery to, are very harsh."
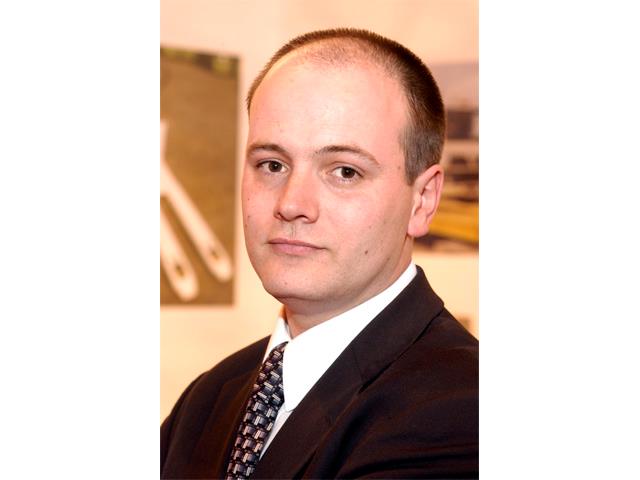 Jonathan Harris ... speed, accuracy vital |
Timotex Ltd, a division of Hawkley International in the UK, manufactures weighing forks, regarded by many as the most accurate, but expensive, system for mobile weighing, and hydraulic scales.
Timotex sales and marketing manager
Jonathan Harris told
Forkliftaction.com News weighing systems were designed to reduce costs and boost the efficiency of customers' operations.
Speed and accuracy were integral to the effective and smooth operation of an efficient warehouse, and until the advent of mobile weighing systems, load weighing represented a time-consuming chore.
Traditional weighing solutions involved the installation of a fixed weighing platform or weighbridge somewhere on-site, but this meant goods had to be transported from the warehouse to the fixed installation, adding more time to each materials handling task.
Harris said traditional methods of weighing were fine for most applications, and indeed necessary, when circumstances limited the variety of systems available for fitment. But when accuracy was paramount - LFT - weighing forks were the only way to go.
"By replacing the forks already fitted to a truck, accuracy to within 0.1% of the applied load can be achieved," he said. "(But) consideration should be given to the simplicity of fitting and the need for minimal maintenance - there is a direct link between efficiency and cost control."
So whether your motivation is accuracy, safety, system versatility or cost, there is a huge range of solutions on offer today in the increasingly sophisticated
world of materials handling. One thing is for certain: mobile weighing systems are all-important in today's logistics environment, and savvy companies will see the benefits such systems can provide.
Stay tuned for part two of our special series on weighing systems, to be published in Forkliftaction.com News #181 on October 28, as we continue our profile of the world market for forklift weighing systems. For advertising enquiries, email www.forkliftaction.com.Did you find this article useful? Let us know!