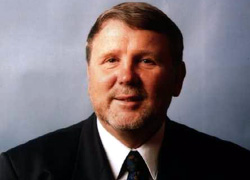 John Cowpe ... no threat |
Electrical energy generation for forklifts is moving into radically new and evolutionary territory, with hydrogen fuel-cell technologies challenging the status quo, writes BERNARD LEVY in the first of this two-part reportLIKE all great ideas in history, man-made technologies inevitably go through their ''sunrise'' and ''sunset'' phases - their rise and fall - and a clear example is the century-old, lead-acid battery widely used in the forklift industry.
Based on two volt cells, today's lead-acid battery is little different in its fundamental technological principles than the original direct current prototype created by two French inventors, Faure and Plante the late 1800s.
Despite some significant advances since World War II, the technology's longstanding commercial dominance is facing being eclipsed by new, "renewable" and "clean" fuel cell alternatives in the new millenium - a challenge being met head-on by the global lead-acid battery sector. Throughout the industrialised world, huge sums of money are being poured into fuel cell research and the development of hydrogen-based power units.
In essence, a fuel cell harnesses the electricity created by the chemical reaction that occurs when hydrogen and oxygen are combined. These are the basic elements of water, and re-form into water once used for power generation. This allows the fuel cell to be marketed as "renewable", "clean" and "environmentally-friendly", as well as providing a potential solution to power shortages and the world's dependence on fossil fuels.
The fuel cell is similar in principle to its lead-acid forerunner, and can be "stacked" together in hundreds to produce enough electrical output to power an industrial vehicle such as a forklift, or a car.
Huge potential benefitsIn North America, General Hydrogen, which has General Motors as one of its main strategic partners, has developed the Hydricity fuel cell which it markets under the futuristic catch-cry: "Breathe easy. The change is coming."
Forklift manufacturer Hyster is also experimenting with the Hydricity technology under an arrangement with General Hydrogen to retrofit fuel cells to some of its machines.
Across the Atlantic, companies such as Carer in Italy, Proton Motor in Germany and many others, are well advanced in developing fuel-cell technologies and about 40 companies throughout the region are now members of German-based Fuel Cell Europe (FCEu).
Part of the World Fuel Cell Council, and backed by the European Commission, FCEu's chief aim is to ensure Europe does not miss out on the enormous commercial, economic and environmental benefits of the new technology.
Several significant hurdles remain in the way of the widespread adoption of fuel cell technology,including hydrogen storage, product cost reduction, durability and infrastructure development.
These difficulties should be overcome within the next two years, but the single greatest obstacle is the cell price.
Optimal cost-efficiencyThe lead-acid battery industry is fighting back hard against the quantum technological advance of fuel cells and the prospect of having a "use-by" date stamped on its own vast product range. At present they have a convincing argument based on cost.
The leading battery manufacturers and suppliers argue that today's sophisticated and sealed, maintenance-free, lead-acid batteries are the most cost effective and efficient for the forklift sector - while at the same time meeting all mandated environmental and workplace health and safety standards.
"Fuel-cell technology is a lot more expensive - not a little more - and the simple reality is that the lead-acid industrial battery is still doing as good a job as is required without costing the end-user a fortune," said
John Cowpe, Exide Technologies Australasia's general manager, sales and marketing, for industrial energy.
"We don't feel threatened because the lead-acid battery is excellent for cycling - 1500 cycles, or five years - and it's capable of taking on a tremendous workload for its size, power and weight. No other product comes anywhere near it - especially in the relatively small sizes used to power most forklifts."
"Let's face it, business people look to the most cost-efficient way of getting a job done - they certainly won't pay up to 10 times more to do the same job," adds Mr Cowpe.
Exide Technologies, with total net sales of around USD2.5 billion in 2003-2004 from its operations in 89 countries, is among the world's largest producers and recyclers of lead-acid batteries, and is a leading player in both the global industrial and transportation sectors.
New 'smart' chargersAnother contentious point of comparison between lead-acid batteries and fuel cells is the maintenance of constant power levels over long periods of usage.
For example, Canadian fuel cell company Cellex claims that while battery-powered forklifts lose approximately 14 per cent of their speed over the last half of the charge, its fuel cell product maintains power at all times at full speed during the entire shift.
The lead-acid industry counters that new "smart" chargers, coupled with sophisticated computerised monitoring technology, can quickly and accurately top up batteries by precisely reading the remaining level of power in the unit. Again, they say, the huge difference in cost makes their solution the most cost-effective.
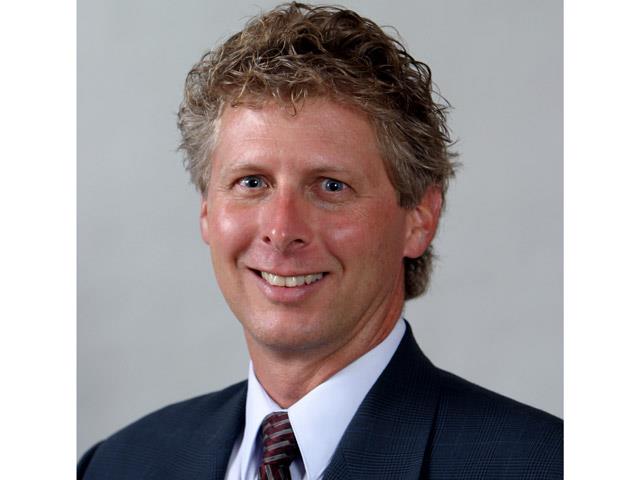 Steve Spaar ... increased productivity |
"The advent of fast charging has eliminated the need for changing batteries and the associated battery handling equipment, loss of productivity and floor space for battery changing and storage rooms," said
Steve Spaar, motive power marketing manager at US-based EnerSys.
"Fast charging utilises modern power electronic technologies to return energy to industrial batteries faster than conventional charging," he said.
"Fast charging delivers 40 amps or more per 100 ampere-hours of battery capacity, which can eliminate the need to change batteries on electric forklifts, thus increasing productivity and reducing costs."
With net sales of close to USD1 billion in 2003-2004, EnerSys is one of the world's largest manufacturers and distributors of industrial batteries, chargers and power equipment, with about 10,000 customers in 100 countries.
The company estimates it held 24 per cent of the USD3.5-billion worldwide lead-acid industrial battery market in 2003, with shares of 30 per cent in North America, 30 per cent in Europe, and 5 per cent in Asia.
Price fall predictedLooking to the future, Spaar conceded fuel cell technologies would offer many advantages to the electric forklift market, but did not necessary threaten the existence of lead-acid batteries in either the short or long term.
"In fact, some fuel cell developers are actually designing fuel cells with lead-acid batteries to help overcome the peak voltage demands imposed on a forklift or truck's power source during lifting and other demanding tasks," he said.
Industry estimates of when fuel cells will become financially viable for warehouse and manufacturing markets, varies from five to 10 years.
However,
Tony Troutt, vice president of business development at General Hydrogen, disagreed. He told Forkliftaction.com he believed the widespread adoption of fuel cell technology would occur around the end of 2006 or early 2007.
"That's the time we expect the cost of our component technologies to come down to a more economical level through large-scale production," Trout said.
"Every year after that, as prices fall, more and more companies will start to see the two to three year pay-back on invested capital that will make it possible for them to migrate from batteries to cell power."
Long-term potentialDavid Hoehn, vice president of sales at Hyster, said he believed a 10-year timeframe for the widespread low-cost availability of fuel cells was more realistic.
"In some cases today, retro-fitting a fork truck with a hydrogen power unit would be two or three times the cost of the truck itself, so that's going to take some time to drop," Hoehn said.
"But once the automotive industry gets heavily involved in fuel cells and they are being produced in big numbers, the prices will begin to come down pretty quickly."
Reach truck marketing director for Raymond Corp,
John Colborn, said that while fuel cell usage was a complex issue requiring significant support infrastructure, the long-term potential for hydrogen technologies was attractive.
"We are currently working with a couple of organisations in this area and will be doing some beta testing in the next year or so and we believe the results will be worthwhile," Colborn said.
"We work on the basis that over a forklift's lifespan, more than 80 per cent of the costs are related to operations and maintenance, while the acquisition costs are just 20 per cent," he said.
"The commercial reality is that anything that reduces total life-cycle costs is well worth considering, above and beyond just the purchase price on its own."
Forkliftaction.com News this week includes more interesting facts and information from the world of industrial batteries and chargers.
Click here to read these items:
* Zinc-air battery challenges conventional rivals
* Europeans unite to ride fuel-cell juggernaut
* Electric and IC forklifts now on 'level playing field'
* Forklift batteries 'lower costs'
* Checklist for charging